Vollständiger Leitfaden zum Zufallsbin-Picking
Was ist Zufallsbin-Picking?
Zufallsbin-Picking ist eine roboterunterstützte Automatisierungsaufgabe, bei der ein Roboter, unterstützt durch eine 3D-Kamera, Objekte aus einem Behälter oder einer Kiste aufnimmt, die zufällig angeordnet sind, unbekannte Orientierungen und ungeordnete Positionen aufweisen. Dieser Prozess wird typischerweise in Fertigungs- und Lagerumgebungen eingesetzt, mit dem Hauptziel, das Abrufen von Artikeln aus einem zufälligen oder ungeordneten Stapel zu automatisieren.
Industrien und Beispiele für Random Bin Picking
Random Bin Picking ist in Branchen von unschätzbarem Wert, in denen das Handhaben und Sortieren von Objekten aus Behältern oder Kisten wiederholend, arbeitsintensiv und zeitaufwendig ist. Nachfolgend sind mehrere Beispiele für Bin-Picking-Anwendungen in verschiedenen Branchen aufgeführt.
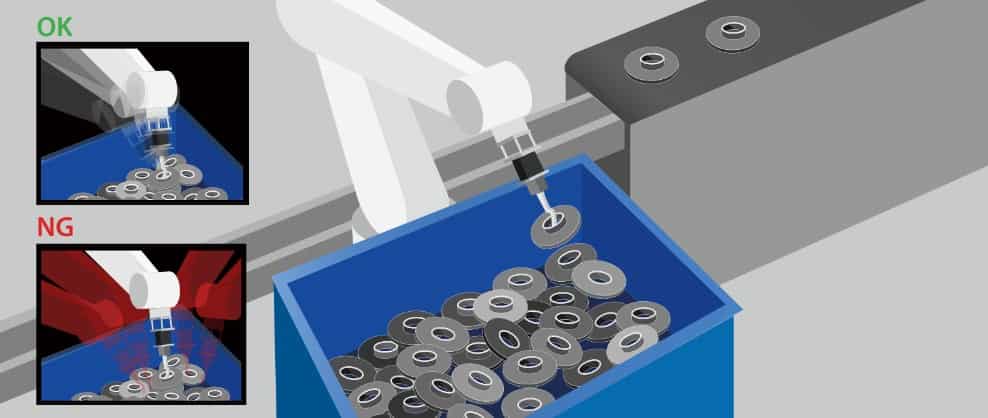
Zufälliges Bin-Picking von Metallobjekten
Logistik
In der Logistik und Lagerhaltung wird das zufällige Bin-Picking verwendet, um zahlreiche Pakete, die zufällig in Behältern positioniert sind, zu sortieren und zu handhaben. Zum Beispiel wurde in einem Projekt für eine globale E-Commerce-Plattform eine Vielzahl von Paketen mit hoher Geschwindigkeit aus Behältern genommen und auf ein Förderband gelegt. Die Hauptaufgabe bestand darin, die hohen Picking-Raten aufrechtzuerhalten, während gleichzeitig schwere Pakete sicher gehandhabt wurden, um Fehler bei der Handhabung oder Schäden zu vermeiden. Die KI-Lösung von Solomon ermöglichte es dem System, schnell zu arbeiten, hohe Durchsatzanforderungen zu erfüllen und gleichzeitig eine genaue und sichere Handhabung von Paketen unterschiedlicher Größen und Gewichte zu gewährleisten.
Automobilindustrie
In der Automobilindustrie wird das zufällige Bin-Picking verwendet, um Automobilkomponenten zu handhaben und zu sortieren. Die Hauptaufgabe für Bin-Picking-Systeme besteht darin, hohe Genauigkeit zu erreichen, um sicherzustellen, dass jedes Teil korrekt klassifiziert, aufgenommen und richtig gestapelt wird. In einem Projekt für einen großen japanischen Autohersteller wurde AccuPick eingesetzt, um Autoteile präzise zu handhaben, Fehler und Mängel in der Montage und Platzierung zu vermeiden und somit die Gesamt-effizienz zu verbessern.
Lebensmittel- und Getränkeindustrie
In der Lebensmittelindustrie spielt das zufällige Bin-Picking eine entscheidende Rolle bei der Automatisierung des Sortierens und Handhabens von Lebensmitteln, was die betriebliche Effizienz erheblich steigert. Eines von Solomons bemerkenswerten Projekten in diesem Bereich war die Zusammenarbeit mit einem führenden multinationalen Süßwarenunternehmen, um verpackte Kekse aus Behältern zu entnehmen und auf ein Förderband zu übertragen. Die Hauptaufgabe bestand im Zykluszeitmanagement, da das System etwa 30 bis 35 Kekse pro Minute aufnehmen und platzieren musste. Die Automatisierung wurde eingeführt, um die körperliche Belastung der Bediener zu reduzieren, wodurch das Risiko von Muskel-Skelett-Erkrankungen verringert und sowohl die Arbeitssicherheit als auch die Effizienz der Produktionslinie verbessert wurden.
Fertigung
Das Bin-Picking wird in der Fertigung häufig eingesetzt, um verschiedene Komponenten zu entnehmen und zu sortieren. Ein führender Hersteller von Industrierobotern und Automatisierungsmaschinen benötigte ein hochgeschwindigkeitsfähiges zufälliges Bin-Picking von spezifischen Metallteilen. Die Hauptanforderungen waren strenge Zykluszeiten und hohe Genauigkeitsvorgaben. Die Objekte mussten an der Ablage-Station gestapelt werden, und jede Ungenauigkeit beim Picking führte zu einer falschen Stapelung. Die Teile konnten aus einer oberen oder hinteren Ansicht mit unterschiedlichen Neigungswinkeln positioniert werden, was eine präzise Erkennung jedes Seitenwinkels durch die KI erforderte. Die glänzende Oberfläche der Metallteile stellte eine zusätzliche Herausforderung für 3D-Kameras dar, da Lichtreflexionen sowohl das 2D-Bild als auch den 3D-Punktwolkenverzerren und die Picking-Genauigkeit verringern konnten. Um dies zu überwinden, wurde anstelle des üblichen weißen Lichts eine SolScan-Industrielle 3D-Kamera mit grünem Projektorlampenlicht verwendet.
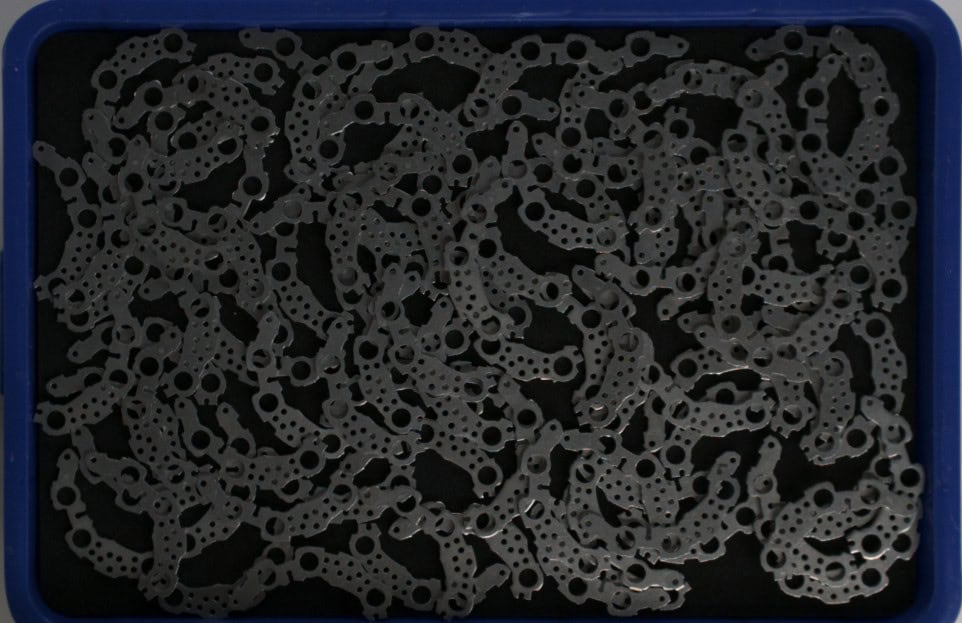
Originales 2D-Bild
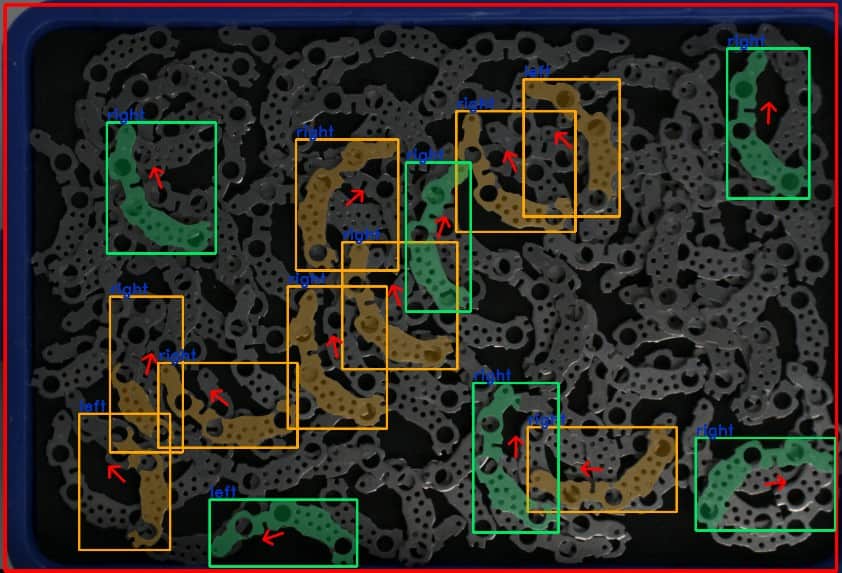
2D KI-Erkennung mit Winkelerkennung
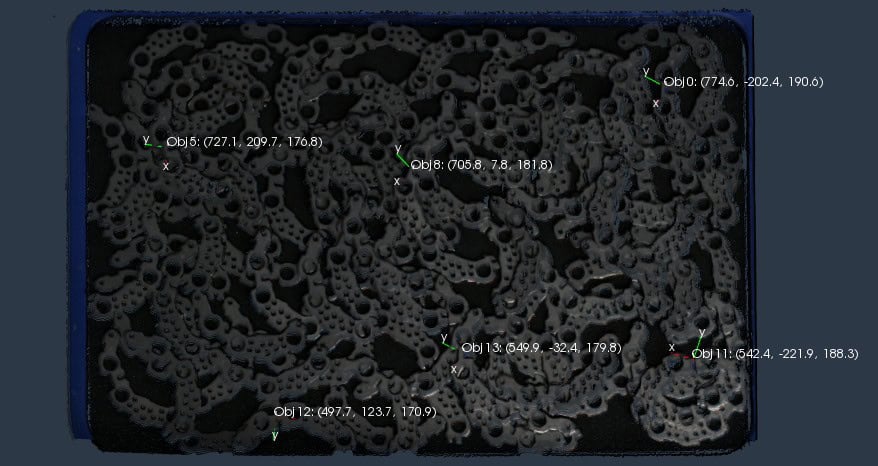
3D-Punktwolke mit Abholpunktplatzierung
Pharmazeutische und medizinische Industrie
Im Bereich Pharmazie und Medizintechnik sind Bin-Picking-Systeme entscheidend für die Handhabung verschiedener Artikel in hochgradig automatisierten und präzisionskritischen Umgebungen. In diesem Fall verwaltete ein pharmazeutischer Distributor verschiedene Behälter, darunter Boxen und Flaschen in unterschiedlichen Formen, Größen und Farben, mit etwa fünf zufällig positionierten und orientierten Objekten pro Bin. Die Hauptanforderung war sicherzustellen, dass der Barcode des Produkts während des Pickvorgangs sichtbar blieb, da die Objekte zwischen den Barcode-Scannern positioniert werden mussten. Der Arbeitsbereich war begrenzt, und die Roboter mussten mit hohen Geschwindigkeiten arbeiten, um strenge Zykluszeiten einzuhalten, was das Risiko von Kollisionen erhöhte. Um dieses Problem zu lösen, kam AccuPick zum Einsatz. Die Software zur Bewegungsplanung berechnete sichere, kollisionsfreie Trajektorien, während die integrierte KI eine hochpräzise Objekterkennung ermöglichte. So konnte der Roboter Objekte aus jeder Position (oben, seitlich oder unten) ohne Verdeckung des Barcodes entnehmen. Zwei unterschiedliche Roboter-Endeffektoren – einer mit einer großen Saugvorrichtung und der andere mit einer kleinen Saugvorrichtung – wurden verwendet. Auf Grundlage der Objekterkennungs-Ergebnisse, der Position und des Typs (Box oder Flasche) wurden strategische Bedingungen und Regeln festgelegt, um sicherzustellen, dass der passende Endeffektor für jedes spezifische Objekt ausgewählt wurde.
Grundlagen des Random-Bin-Picking-Systems
Tool Center Point (TCP) Kalibrierung
Die TCP-Kalibrierung des Roboters muss durchgeführt werden, sobald ein Endeffektor für die Anwendung ausgewählt und am Flansch des Roboters montiert ist. Der TCP dient als Referenzpunkt, um dem Roboter die genaue Position und Ausrichtung des Endeffektors zu vermitteln.
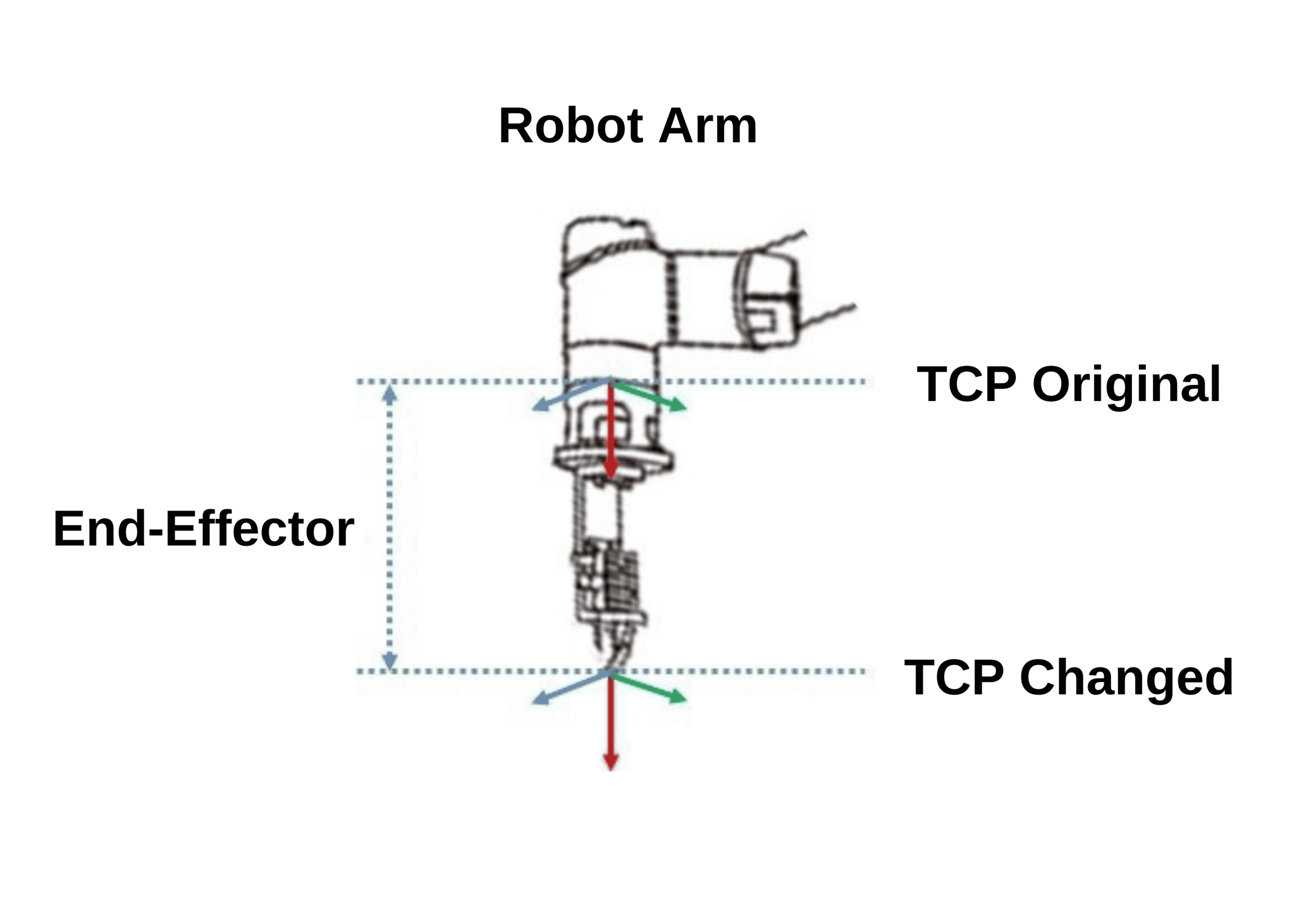
TCP-Kalibrierung
Vision-zu-Roboter-Kalibrierung
Die Kalibrierung zwischen dem Vision-System und dem Roboter ist unerlässlich. Da der Ursprung des Koordinatensystems der 3D-Kamera an der Basis der Kamera liegt und der Ursprung des Koordinatensystems des Roboters an der Basis des Roboters, ermöglicht die Kalibrierung dem Roboter, das Koordinatensystem der Kamera zu verstehen und diese Koordinaten in sein eigenes System zu konvertieren. Dadurch werden alle Positions- und Rotationskoordinaten, die vom 3D-Scanner an den Roboter gesendet werden, genau interpretiert, sodass der Roboter den spezifischen Punkt mit der erforderlichen Position und Rotation erreichen kann.
3D-Scanning und Objekterkennung
Der 3D-Scanner erfasst sowohl 2D-Bilder als auch 3D-Punktwolken der Objekte im Behälter. Diese Daten werden verwendet, um einen Abholpunkt für Objekte zu erzeugen, die die grundlegenden Kriterien für das Abholen erfüllen. Diese Kriterien können je nach Projekt variieren, beinhalten jedoch in der Regel:
• Objekte, die sich auf der oberen Oberfläche des Behälters befinden.
• Objekte, die nicht verdeckt oder nur leicht von anderen Gegenständen verdeckt sind.
• Sichtbare Merkmale, die bei der Bestimmung der Abholorientierung des Objekts helfen.
• Objekte sind sicher positioniert und gedreht, um sicherzustellen, dass der Roboter oder sein Endeffektor während des Abholvorgangs nicht kollidiert.
• Objekte, die sich auf der oberen Oberfläche des Behälters befinden.
• Objekte, die nicht verdeckt oder nur leicht von anderen Gegenständen verdeckt sind.
• Sichtbare Merkmale, die bei der Bestimmung der Abholorientierung des Objekts helfen.
• Objekte sind sicher positioniert und gedreht, um sicherzustellen, dass der Roboter oder sein Endeffektor während des Abholvorgangs nicht kollidiert.
Erzeugung und Ausführung des Abholpunkts
Der Abholpunkt für jedes Objekt umfasst in der Regel sowohl Positionals- als auch Rotationskoordinaten. Sobald der Abholpunkt generiert wurde, empfängt der Roboter diese Informationen. Der Robotercontroller berechnet daraufhin die Trajektorie, um den Abholpunkt zu erreichen. Für anspruchsvollere Anwendungen in Umgebungen, die eine Kollisionsvermeidung erfordern, ist eine Bewegungsplanungssoftware erforderlich, um eine sichere Trajektorie zu berechnen. Beim Erreichen des Abholpunkts nimmt der Roboter das Objekt auf und legt es dann an dem gewünschten Ort oder in dem gewünschten Behälter ab.
Zykluswiederholung
Sobald alle erkannten Objekte im aktuellen Zyklus aufgenommen und abgelegt wurden, beginnt ein neuer Zyklus mit dem Scanvorgang. Dies gewährleistet einen kontinuierlichen Betrieb, bis der Behälter leer ist.
Herausforderungen und Lösungen beim Random Bin Picking
Strikte Zykluszeitanforderungen
Projekte mit strengen Zykluszeitanforderungen stehen vor erheblichen Herausforderungen, da jeder Schritt schnell abgeschlossen werden muss, um die Gesamtziele zu erreichen. Wichtige Überlegungen umfassen:
• 3D-Kamera-Aufnahmezeit: Die 3D-Kamera muss schnell sowohl 2D-Bilder als auch 3D-Punktwolken erfassen.
• Erzeugung von Bildern und Punktwolken: Algorithmen zur Erzeugung der 2D-Bilder und 3D-Punktwolken müssen effizient und optimiert sein.
• Objekterkennung: Der Algorithmus zur Objekterkennung muss schnell sein; der Einsatz von KI kann die Geschwindigkeit und Genauigkeit erheblich steigern.
• Pick-Point-Positionierung: Der Algorithmus zur Bestimmung der Pick-Punkte muss schnell sein. KI kann hier eingesetzt werden, um hohe Geschwindigkeit zu erreichen.
• Bewegungsplanung: Das Bewegungsplanungssystem muss sicherstellen, dass sichere Trajektorien schnell berechnet werden.
• Robotergeschwindigkeit: Der Roboter selbst muss mit hoher Geschwindigkeit arbeiten, um den Zykluszeitanforderungen gerecht zu werden.
• Endeffektor-Auswahl: Die Auswahl des geeigneten Endeffektors ist entscheidend, um Fehlpickvorgänge zu minimieren und sicherzustellen, dass die Objekte während der Roboterbewegungen sicher bleiben.
• 3D-Kamera-Aufnahmezeit: Die 3D-Kamera muss schnell sowohl 2D-Bilder als auch 3D-Punktwolken erfassen.
• Erzeugung von Bildern und Punktwolken: Algorithmen zur Erzeugung der 2D-Bilder und 3D-Punktwolken müssen effizient und optimiert sein.
• Objekterkennung: Der Algorithmus zur Objekterkennung muss schnell sein; der Einsatz von KI kann die Geschwindigkeit und Genauigkeit erheblich steigern.
• Pick-Point-Positionierung: Der Algorithmus zur Bestimmung der Pick-Punkte muss schnell sein. KI kann hier eingesetzt werden, um hohe Geschwindigkeit zu erreichen.
• Bewegungsplanung: Das Bewegungsplanungssystem muss sicherstellen, dass sichere Trajektorien schnell berechnet werden.
• Robotergeschwindigkeit: Der Roboter selbst muss mit hoher Geschwindigkeit arbeiten, um den Zykluszeitanforderungen gerecht zu werden.
• Endeffektor-Auswahl: Die Auswahl des geeigneten Endeffektors ist entscheidend, um Fehlpickvorgänge zu minimieren und sicherzustellen, dass die Objekte während der Roboterbewegungen sicher bleiben.
Hohe Pick-Genauigkeit
Hohe Picking-Genauigkeit ist entscheidend für effektives Random-Bin-Picking. Wichtige Überlegungen umfassen:
• Geeigneter 3D-Scanner: Die Auswahl eines 3D-Scanners, der für das Material des Objekts, den Arbeitsabstand und die Dimensionen des Behälters geeignet ist, ist unerlässlich.
• Hohe Auflösung: Der 3D-Scanner sollte eine hohe Auflösung für eine detaillierte Erfassung bieten.
• Computer Vision und Bildvorverarbeitung: Der Einsatz fortschrittlicher Computer Vision-Techniken und Bildvorverarbeitung kann die Genauigkeit erheblich verbessern.
• KI zur Objekterkennung: Die Auswahl des richtigen KI-Algorithmus kann die Genauigkeit der Objekterkennung verbessern.
• KI zur Pick-Point-Platzierung: KI-Methoden zur 3D-Abgleichung können die Genauigkeit der Pick-Point-Platzierung weiter verfeinern.
• Feinabstimmung: Eine umfassende Feinabstimmung der 3D-Scanner-Parameter, der Bildvorverarbeitungstechniken, des 2D-Erkennungs-KI-Algorithmus und der 3D-Abgleichmethode für die Pick-Point-Platzierung ist entscheidend für optimale Leistung.
• Stabile Lichtverhältnisse: Die Sicherstellung einer stabilen Beleuchtungsumgebung ist wichtig, um konsistente Ergebnisse zu erzielen.
• Geeigneter 3D-Scanner: Die Auswahl eines 3D-Scanners, der für das Material des Objekts, den Arbeitsabstand und die Dimensionen des Behälters geeignet ist, ist unerlässlich.
• Hohe Auflösung: Der 3D-Scanner sollte eine hohe Auflösung für eine detaillierte Erfassung bieten.
• Computer Vision und Bildvorverarbeitung: Der Einsatz fortschrittlicher Computer Vision-Techniken und Bildvorverarbeitung kann die Genauigkeit erheblich verbessern.
• KI zur Objekterkennung: Die Auswahl des richtigen KI-Algorithmus kann die Genauigkeit der Objekterkennung verbessern.
• KI zur Pick-Point-Platzierung: KI-Methoden zur 3D-Abgleichung können die Genauigkeit der Pick-Point-Platzierung weiter verfeinern.
• Feinabstimmung: Eine umfassende Feinabstimmung der 3D-Scanner-Parameter, der Bildvorverarbeitungstechniken, des 2D-Erkennungs-KI-Algorithmus und der 3D-Abgleichmethode für die Pick-Point-Platzierung ist entscheidend für optimale Leistung.
• Stabile Lichtverhältnisse: Die Sicherstellung einer stabilen Beleuchtungsumgebung ist wichtig, um konsistente Ergebnisse zu erzielen.
Zufällige Objektorientierung
Objekte in Behältern haben oft zufällige Anordnungen, unbekannte Ausrichtungen und unstrukturierte Positionen. Diese Zufälligkeit kann dazu führen, dass sich Objekte gegenseitig behindern. Um diese Herausforderungen zu überwinden, können verschiedene Strategien angewendet werden:
• Schichtweise Vorgehensweise: Scannen und Auswählen der am besten geeigneten Objekte, dann erneutes Scannen, um die nächste Iteration zu starten und schrittweise Schicht für Schicht vorzugehen.
• Behälterschüttler: Ein Behälterschüttler kann verwendet werden, um die Positionen der Objekte zu verändern.
• Zwei-Stufen-Picking: Zunächst das Objekt so effektiv wie möglich greifen und dann an einer zweiten Station ohne andere Objekte trennen, um eine genauere Entnahme zu ermöglichen.
• Endeffektor: Die richtige Auswahl des Endeffektors ist entscheidend, um die Wahrscheinlichkeit einer erfolgreichen Objektaufnahme in herausfordernden Szenarien zu erhöhen.
• Behälterdesign: Das Design des Behälters ist entscheidend. Für bestimmte Anwendungen kann eine umgekehrte, truncated Pyramidform des Behälters eine effektive Lösung bieten.
• Schichtweise Vorgehensweise: Scannen und Auswählen der am besten geeigneten Objekte, dann erneutes Scannen, um die nächste Iteration zu starten und schrittweise Schicht für Schicht vorzugehen.
• Behälterschüttler: Ein Behälterschüttler kann verwendet werden, um die Positionen der Objekte zu verändern.
• Zwei-Stufen-Picking: Zunächst das Objekt so effektiv wie möglich greifen und dann an einer zweiten Station ohne andere Objekte trennen, um eine genauere Entnahme zu ermöglichen.
• Endeffektor: Die richtige Auswahl des Endeffektors ist entscheidend, um die Wahrscheinlichkeit einer erfolgreichen Objektaufnahme in herausfordernden Szenarien zu erhöhen.
• Behälterdesign: Das Design des Behälters ist entscheidend. Für bestimmte Anwendungen kann eine umgekehrte, truncated Pyramidform des Behälters eine effektive Lösung bieten.
Unvollständige Picking-Genauigkeit
Trotz der Leistungsfähigkeit fortschrittlicher Vision-Systeme kann die Picking-Genauigkeit nicht immer 100% betragen. Objekte, die sich am Boden, an den Rändern oder in den Ecken des Behälters befinden, können aufgrund ihrer Position unentdeckt bleiben. In solchen Fällen kann der Einsatz eines Bin-Shakers, um die Objekte in zugänglichere Bereiche des Behälters zu bewegen, eine effektive Lösung darstellen.
Begrenzter Arbeitsbereich und hohe Roboter-Geschwindigkeit
In engen Räumen, in denen eine hohe Roboter-Geschwindigkeit erforderlich ist, ist eine Bewegungsplanungssoftware unerlässlich. Eine leichtgewichtige CAD-Datei des Arbeitsbereichs und des Endeffektors kann erforderlich sein, die das Roboter-Modell enthält, um potenzielle Trajektorien zu simulieren und den sichersten Weg zu berechnen.
Transparente oder glänzende Objekte
Transparente oder glänzende Metallobjekte stellen zusätzliche Herausforderungen bei der Erstellung einer genauen Punktwolke für die Pick-Point-Platzierung dar. Lösungen umfassen den Einsatz von KI, Computervision und Bildvorverarbeitungstechniken sowie die Verwendung eines hochwertigen 3D-Scanners. Die Kombination von Methoden wie Stereo-Vision und strukturiertem Projektorlicht sowie Optionen für unterschiedliche Lichtfarben, hohe Auflösung und erhöhte Lichtintensität kann effektiv helfen, diese Herausforderungen zu bewältigen.
Zufälliges Bin Picking mit KI
KI spielt eine entscheidende Rolle bei der Erreichung einer hochwertigen Erkennung und präzisen Pick-Point-Platzierung, während gleichzeitig wettbewerbsfähige Zykluszeiten in industriellen Anwendungen eingehalten werden. In Kombination mit Computer Vision und Bildvorverarbeitungstechniken kann sich KI an verschiedene Umweltbedingungen und Objektorientierungen anpassen. Diese Anpassungsfähigkeit macht KI besonders geeignet für Anwendungen im Bereich des zufälligen Bin Pickings, bei denen Objekte zufällig angeordnet sind. KI-Modelle, die für diese Szenarien entwickelt wurden, sollten robust und flexibel sein, um verschiedene Pick-Herausforderungen zu bewältigen.
Zufälliges Bin Picking, unterstützt von KI und fortschrittlichen Vision-Systemen, revolutioniert die industrielle Automatisierung in verschiedenen Sektoren. Entdecken Sie, wie Solomons KI- und 3D-Vision-Lösungen Ihre Betriebsabläufe optimieren können.