What is AOI?
What Does AOI Stand For
Introduction to AOI
Key Components of AOI Systems
Industries and Applications of AOI Technology
The demand for improved yield in the manufacturing industry has increased due to the potential impact of defects on product functionality. Traditional production lines relying on manual defect detection methods are no longer able to meet the requirements for comprehensive inspection and production efficiency. Consequently, the adoption of AOI systems has become the mainstream approach for defect detection in industrial processes.
Key Specifications to Consider for AOI Systems
Speed
Refers to the number of inspections conducted per minute or the ability to inspect a specific length within a given time frame.
Accuracy
Specifies the required level of measurement precision, such as detecting dimensions with an accuracy of 5µm or 0.005mm.
Field of View (FOV)
Denotes the visible range captured by the camera during the inspection process.
Benefits of AOI in Manufacturing
Reduced Manual Inspection
AOI provides more precise and consistent defect judgment compared to human visual inspection or manual inspection using optical instruments.
Improved Inspection Speed
AOI systems equipped with high-resolution cameras can detect details that are difficult for the naked eye to recognize. They also overcome the efficiency limitations of traditional manual visual inspection methods.
Consistent Quality Control
AOI systems provide uniform defect detection, ensuring that every part is inspected with the same level of precision, reducing human error.
Reduced Labor Costs
By automating the inspection process, AOI systems reduce the need for manual labor, which can lower overall operational costs.
Challenges and Limitations of AOI Systems
Complex Setup and Customization
AOI systems can be complex and highly customized, making their setup and operation challenging. They face difficulties in handling complex product defects, image backgrounds, and lighting variations.
False Positives and Overkill Detection
AOI is based on traditional algorithms often set with strict parameters. This can result in overkill or false-positive results due to sensitivity to external conditions such as lighting variations. Consequently, additional manual inspection is often necessary to mitigate false positives.
Complex and Irregular Defects
AOI systems may face challenges in accurately identifying and classifying complex defects that require advanced image processing techniques. Irregular shapes, subtle defects, or defects in hard-to-reach areas can pose difficulties for AOI systems.
Dependence on Predefined Defect Parameters
AOI relies on rule-based decision-making mechanisms that depend on predefined parameters to detect sample defects. This can lead to leakage issues where defects that don’t conform to the defined parameters may be missed.
Equipment and Conditions Requirements
AOI heavily relies on the proper combination of light sources, cameras, and lenses. The setup needs to consider the material, color, and shape of the object to enhance contrast and obtain suitable images.
High Cost and Maintenance Requirements
AOI systems can be expensive to acquire and maintain. The initial investment includes specialized equipment such as high-resolution cameras and advanced software. Regular maintenance and calibration are also necessary to ensure optimal performance.
The Role of AOI in Modern Manufacturing
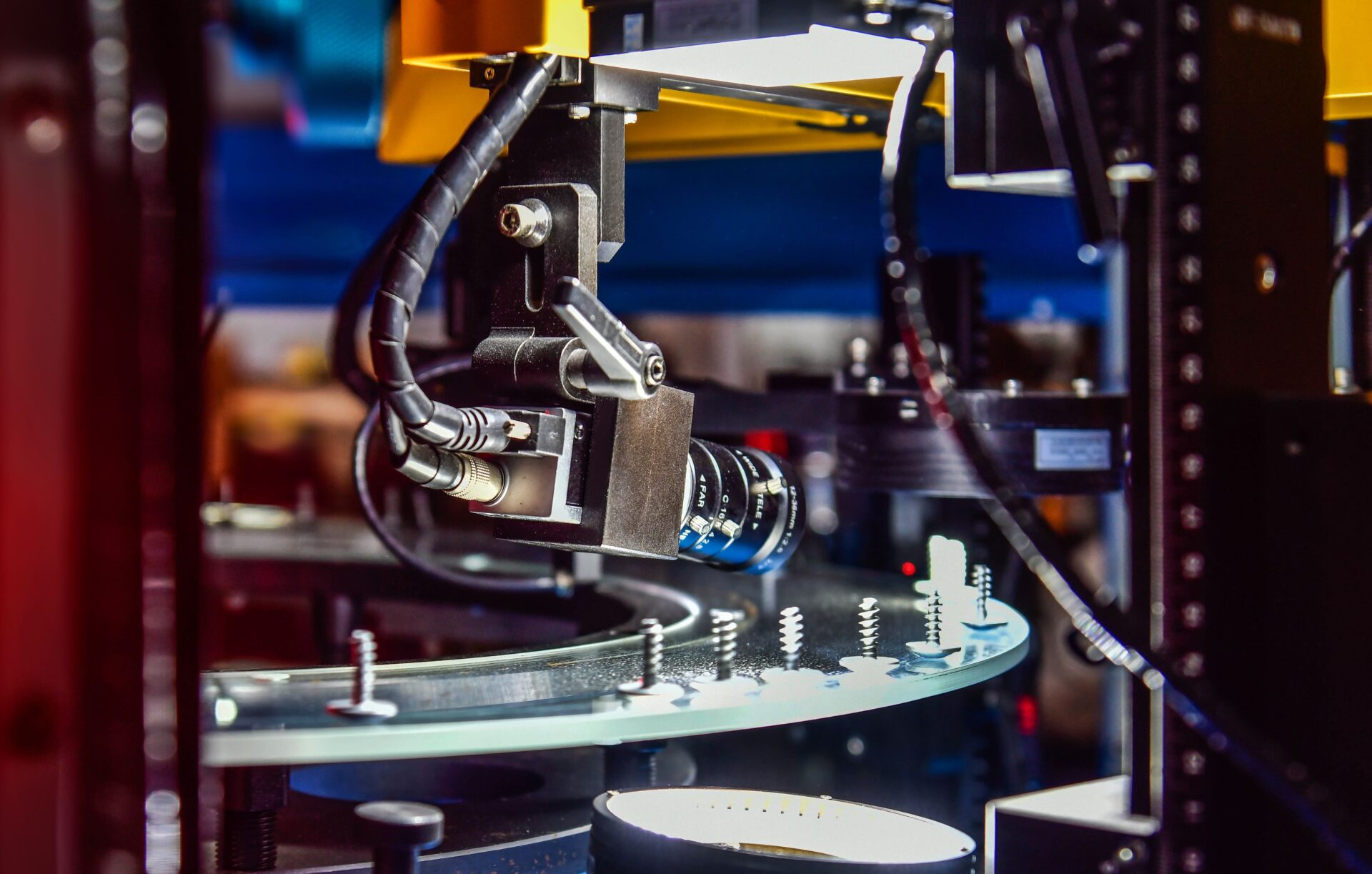