AI と AOI の違いは何でしょうか?
ぞれのメリット・デメリットや応用例にはどのようなものがありますか?
従来の「少品種・大量生産」から、現在では「多品種・少量生産」へと変化し、生産の柔軟性が求められるようになりました。それに伴い、検査対象のサイズ、形状、材質などの複雑性が増し、定義が曖昧な欠陥も発生するようになっています。従来の AOI では、まず欠陥サンプルを定義し、設定されたパラメータを基準に判定を行いますが、柔軟かつ迅速な判断が難しく、見逃し率の大幅な増加につながっています。このような状況の中、AI の台頭によりマシンビジョンが進化し、「擬人化」技術が新たな解決策として注目されています。
AOI 検査システムは、工業製造プロセスにおける欠陥識別の主流となっている
消費者向け電子製品が次々と登場する中、半導体、ディスプレイ、光電、エネルギー、通信などの製造業も発展を遂げており、製品検査の方法にも大きな変化が生じています。あらゆる部品の欠陥が製品の機能に影響を及ぼす可能性があるため、製造業では歩留まり向上の需要がますます高まっています。従来の生産ラインでは、大量の人手を頼りに製品の欠陥を検査していましたが、全数検査と生産効率の要求を満たすことが困難になってきました。そのため、AOI(自動光学検査)システムの導入が、工業製造プロセスにおける欠陥識別の主流となっています。AOIとは何か、その利点についてはこちらをご覧ください。
AOIシステムは、マシンビジョンを核とし、光学、電気制御、機構設計、および検査ソフトウェアを組み合わせて検査作業を実行します。光源配置によって画像の特徴を強調し、コンピュータの画像処理技術を活用して位置特定や検査を行い、生産ライン上の完成品や半完成品の欠陥、異物、その他の異常を迅速に検出します。人手による検査と比較して、AOIシステムは欠陥判定の基準がより一貫しています。さらに、高解像度カメラを搭載したAOIシステムは、人の目では識別が難しい細部まで検査可能であり、1分間に数千件ものスクリーニングができるため、従来の目視検査の低効率という課題を改善します。
AOI(自動光学検査)による欠陥検出は、製造業において非常に広く適用されています
AOIは製造業での応用が非常に広範であり、製品における変形、破損、部品の欠落、汚れや傷などの欠陥の検出や、バーコード読み取り、位置合わせ、精密測定、印刷検査(図1のような )、などもAOI技術で行うことができます。したがって、半導体、プリント基板(PCB)、パネル、電子機械、繊維、食品加工、自動車などの業界でその姿を見ることができ、特にPCBとパネル業界では主に使用されています。
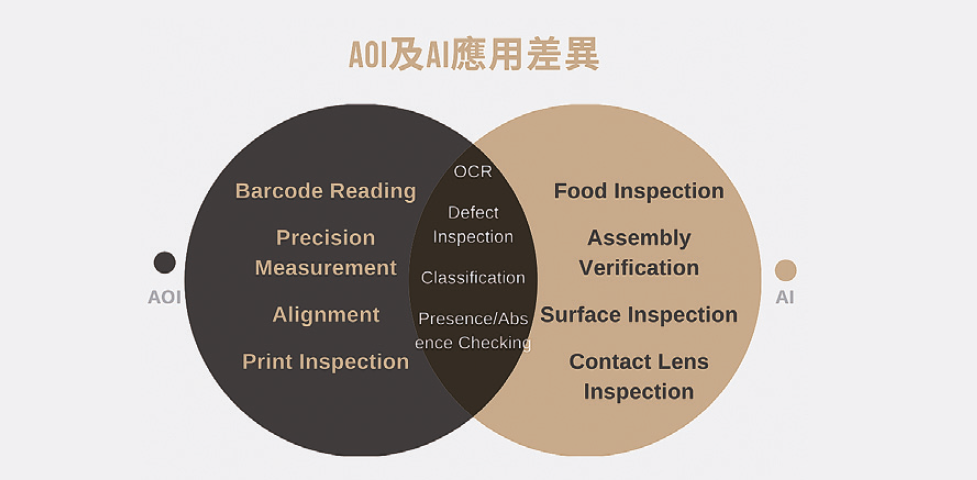
AOIはAIの自主学習能力を欠いており、そのため検査において課題に直面しています
AOIシステムは多くの製造業の生産ラインに広く導入されていますが、その高度にカスタマイズされた特性により、導入の難易度や制限が依然として存在します。複雑な製品の欠陥や画像の背景、光の変化に直面すると、AOIシステムの使用は相対的に制限されます。
AOIはルールベースの判断メカニズムを採用しており、プログラム言語で検出ロジック(ルール)を記述して、定義されたパラメーターを基準にサンプルの欠陥を検出します。例えば、検出ロジックが欠陥を円形として定義した場合、円形でない欠陥はAOIシステムで異常として検出されません。このため、漏検(リーク)問題が発生することがよくあります。例えば、PCBA異常欠陥検出、プラスチッククリップの欠陥検査、金型油汚れの金属プレス部品の傷検査など、ランダムに発生する欠陥タイプはすべてAOIシステムの弱点となります。
欠陥の漏検を避けるために、AOIシステムはしばしばパラメータを非常に厳格に設定し、その結果、システムが過剰に敏感になり、光の影響など外的条件によって誤検出(オーバーキル)が発生しやすくなります。エンジニアはアルゴリズムやパラメータを継続的に調整する必要があり、また、生産ラインには漏検や誤検出を防ぐために人員を配置し、製品の再検査を行う必要があります。これにより、生産効率が大きく影響を受け、製造コストが増加します。
AOIは光源、カメラ、レンズの三者の緊密な連携に大きく依存しています。例えば、光源に関しては、物体の特徴を強調しコントラストを高めるために、検査対象の材質、色、形状に応じた光の強度や特性を設計し、適切な画像を取得することで誤検出のリスクを低減する必要があります。カメラを選択する際には、検査の要件に基づいてイメージセンサー、解像度、フレームレートなどを決定し、適切なレンズと組み合わせることで、光学システムの性能を最大限に発揮できます。まさに「一つが崩れると全体に影響する」システムと言えるでしょう。
設備の細かい仕様が画像品質に影響を与えるだけでなく、機械の調整や部品の交換が発生した場合、エンジニアが過去の経験をもとに機械のパラメータ設定や位置調整をやり直す必要があります。さらに、ソフトウェアとハードウェアの調整プロセスは比較的複雑であり、修理期間は短くても数日、長ければ数ヶ月に及ぶこともあります。これにより、スマート製造の生産ラインが求める柔軟性に対応することが難しくなります。そのため、近年ではAOIを導入している製造業者が、検査効率の向上を目的にAOIとAIの統合を進めています。詳しくはこちらをご覧ください。
AIによる欠陥検出がAOIを強化し、スマート製造への転換の鍵となる
AI深度学習技術による欠陥検出と従来のAOIの最大の違いは、「経験則」にあります。AIはまるで新米の職人のように、ある程度ベテラン技術者の検査能力を模倣することができます。大量の有効なデータを活用し、AI深度学習技術を用いてシステムモデルを迅速に訓練することで、欠陥の範囲や異常検出モデルを自動的に定義し、最適なOK・NGパラメータを見つけ出します。これにより、未知の欠陥を効果的に判断し、検査基準の一貫性を確保するとともに、識別精度を大幅に向上させることができます(図2参照)。
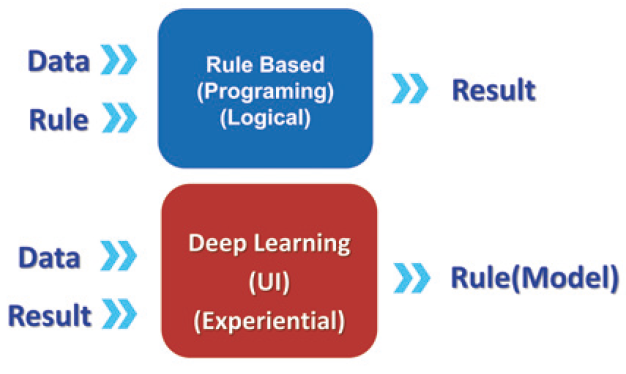
各業界におけるドメイン知識(Domain Knowledge)の違いが大きいため、従来のAOIエンジニアが業界向けにAOIシステムを開発する際、現場の課題を迅速に解決することは困難です。そのため、業界経験を持つ作業員と何度もやり取りを行い、適切なAOIハードウェアやAOIルールを設計する必要があります。
一方、AI瑕疵検出システムは、インターフェースを通じて画像内のどの特徴が検査対象となるかを学習し、その後、システム自体が自動的に検査ルールを生成します。このため、従来のAOIと比べ、学習効率や実行力において大きな違いがあります。
もちろん、深層学習を活用することで検査精度を向上させるだけでなく、AI技術は検査結果が光源の影響を受ける問題を大幅に軽減します。従来のAOIは、光の強さや撮影角度、影や反射、検査対象の材質や形状(例:半透明素材や金属の曲面)などの条件に大きく左右され、正確な識別が困難でした。一方で、AI瑕疵検出は光源への依存度が低く、光が安定していれば、輪郭や形状が多少ぼやけていても、また金属の反射による干渉があっても、適切に検査・分類を行うことが可能です。
AI瑕疵検出は、複雑な表面や外観上の欠陥の検出に優れており、例えば反射する物体の凹みや傷(図3参照)を正確に識別できます。また、変形したり識別しにくい文字に対しても、光学文字認識(Optical Character Recognition, OCR)を適用することが可能です。さらに、予測不可能なパターンや欠陥の検出にも対応しており、欠陥の色やサイズが不均一であったり、大きく変形していたり、複雑な形状でランダムに分布していたりしても、AIはデータ分析に基づいて欠陥の位置を判断できます。そのため、分析速度・精度・人件費の面でも、ルールベースの従来のアルゴリズムでは対応が難しい複雑な検査や分類の課題を、深層学習によって克服できる可能性があります。
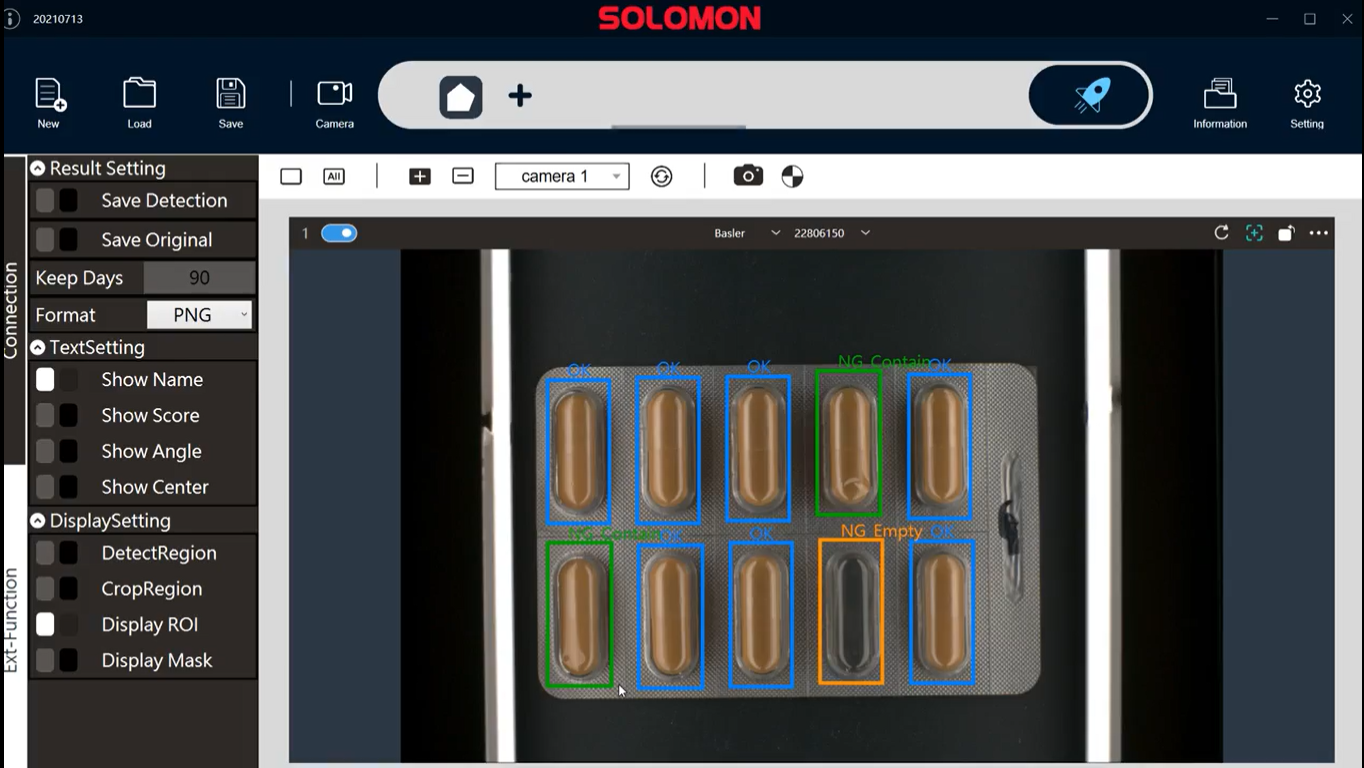
(図3:ブリスター包装(PTP)ラインでは、1時間あたり約5,000~40,000錠の錠剤やカプセルが包装されますが、充填時に誤差が生じることがあり、その結果、ブリスター内に内容物が入っていない、不良品が混入している、またはカプセルの粉末が漏れ出すといった欠陥が発生することがあります。各種欠陥の画像サンプルを用いてAIモデルを訓練することで、各ブリスターの包装・充填状況をリアルタイムかつ迅速に識別し、適切に分類・マーキングすることが可能になります。)