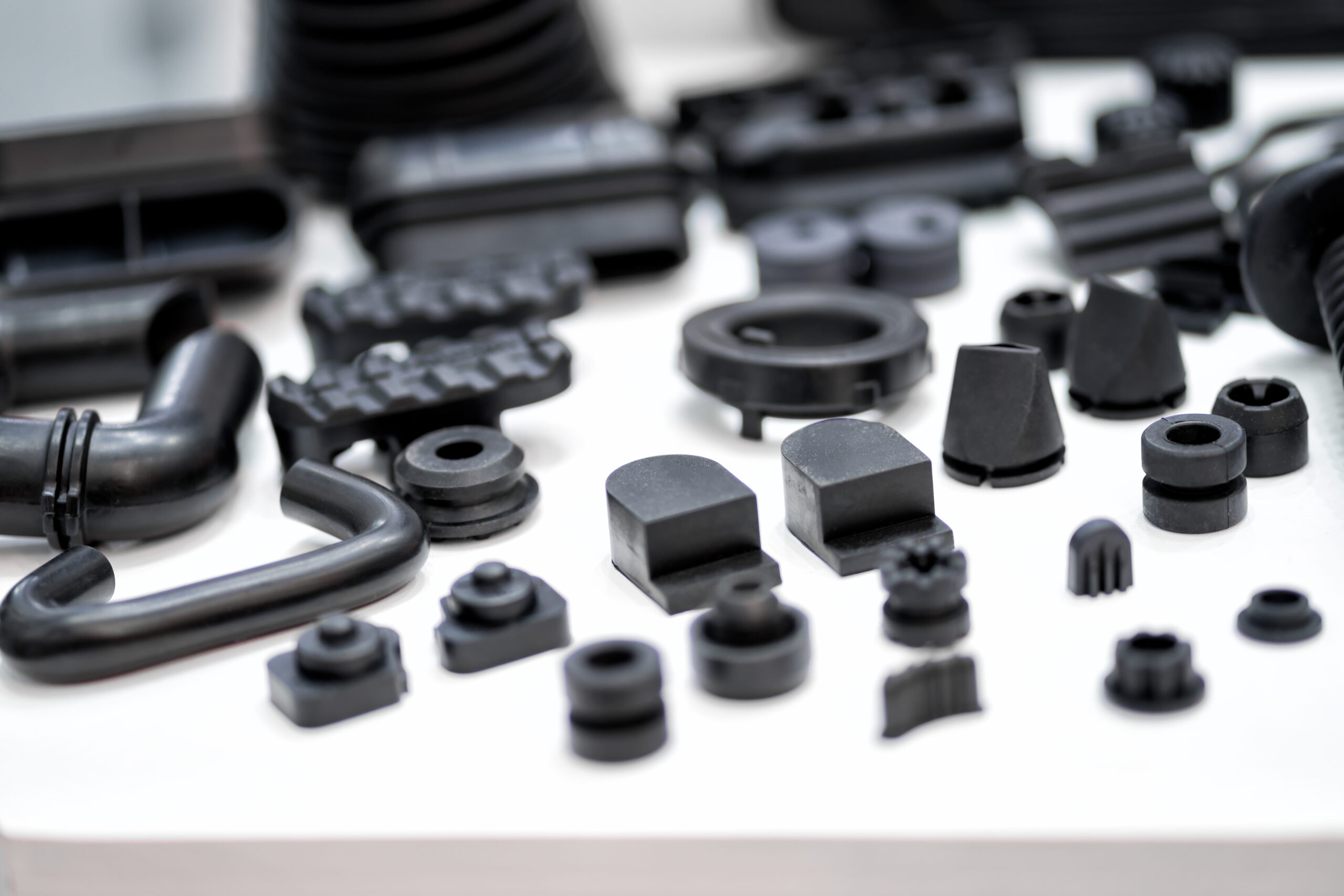
META-aiviFallstudie
Überwachung der Spritzgussmaschine mit IP-Kameras
Kunde
Der Kunde ist ein internationaler Hersteller von Kunststoffen für die Automobilindustrie.
Fall
Automatisierung der Fehlermeldung von Spritzgussmaschinen
Um die Präzision der Spritzgussfertigung zu optimieren, benötigte der Kunde eine Lösung zur Einrichtung eines zuverlässigen und effizienten automatisierten Erkennungssystems. Zuvor auf manuelle Aufsicht angewiesen, riskierte der ursprüngliche Prozess Ausfallzeiten und hohe Wartungskosten. Unsere Lösung automatisiert die Erkennung, signalisiert der Maschine, das Schließen zu vermeiden und einen neuen Formeinsatz zu starten, wenn der Pin ausgefahren ist. Dieser Wechsel von manueller zu automatisierter Erkennung verbessert die betriebliche Effizienz, minimiert Ausfallzeiten und steigert die Produktionszuverlässigkeit.
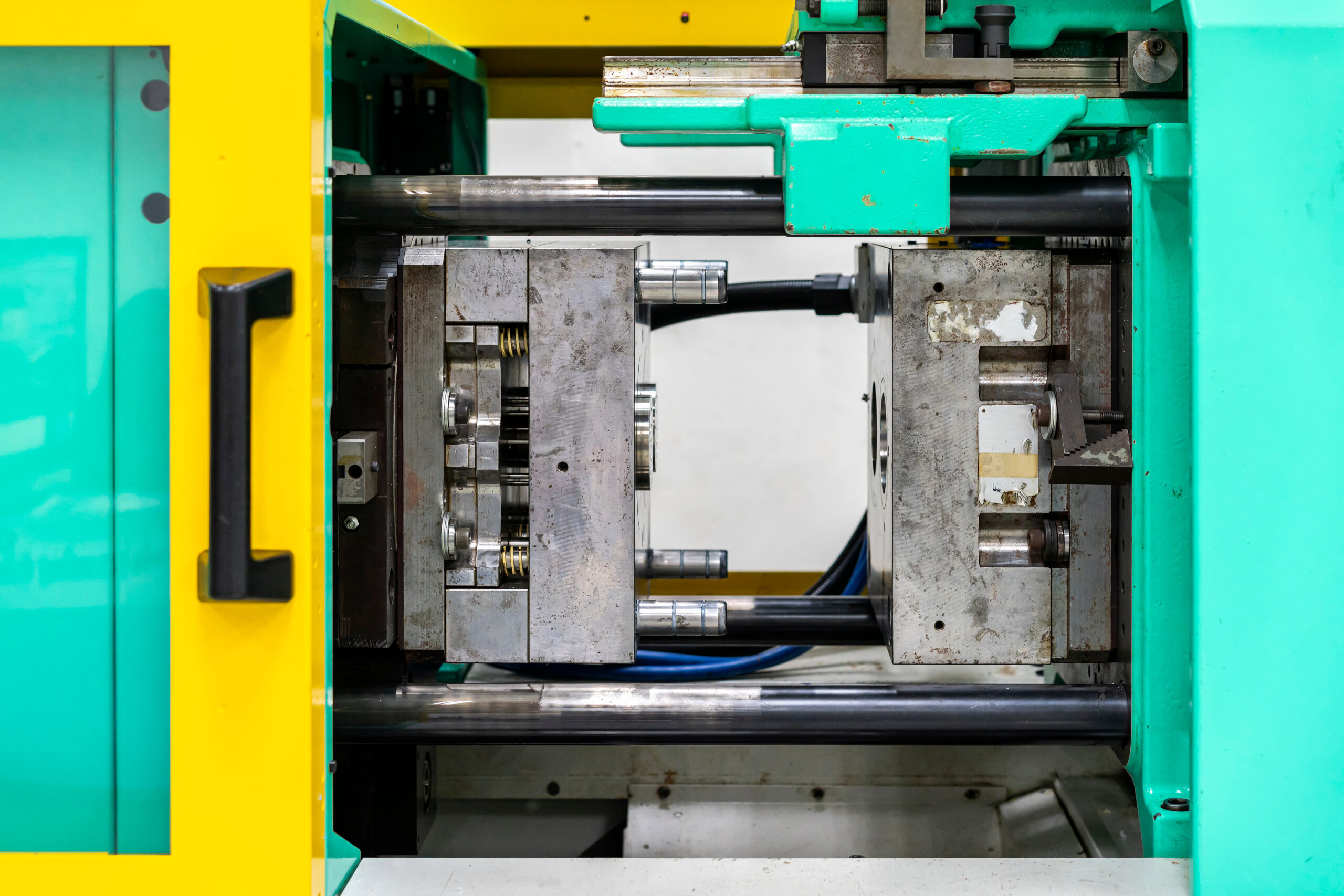
Herausforderung
Maschinenkonnektivität und Systemintegration
Der Kunde stieß auf Herausforderungen aufgrund des Fehlens einer smarten Konnektivität bei der Spritzgussmaschine. Dies erschwerte die Implementierung eines automatisierten Ejektor-Pin-Erkennungssystems und beeinträchtigte die Echtzeitkommunikation und Datentransfer-Effizienz. Zudem erschwerte das Fehlen eines integrierten Steuerungssystems die Integration der Lösung zur Fehlererkennung, was zu Maschinenfehlern, häufigen Wartungsarbeiten und störenden Produktionsausfällen führte.
Lösung
Fehlererkennung der Maschine mit IP-Kameras
Um die Herausforderungen der Konnektivität und Steuerung zu überwinden, implementierten wir eine innovative Lösung, bei der META-aivi KI-Bilderkennung in Verbindung mit einer IP-Kamera verwendet wird, um das Schließen der Form in Echtzeit zu erkennen. Falls der Ejektor-Pin nicht zurückgezogen wird, sendet das System sofort eine Benachrichtigung und pausiert die Maschine, um die Betriebssicherheit zu gewährleisten und Störungen zu minimieren. Diese vereinfachte Lösung automatisiert nicht nur die Fehlermeldung, sondern steigert auch die Produktionseffizienz, indem sie den Bedarf an manueller Aufsicht reduziert und ungeplante Ausfallzeiten verhindert.