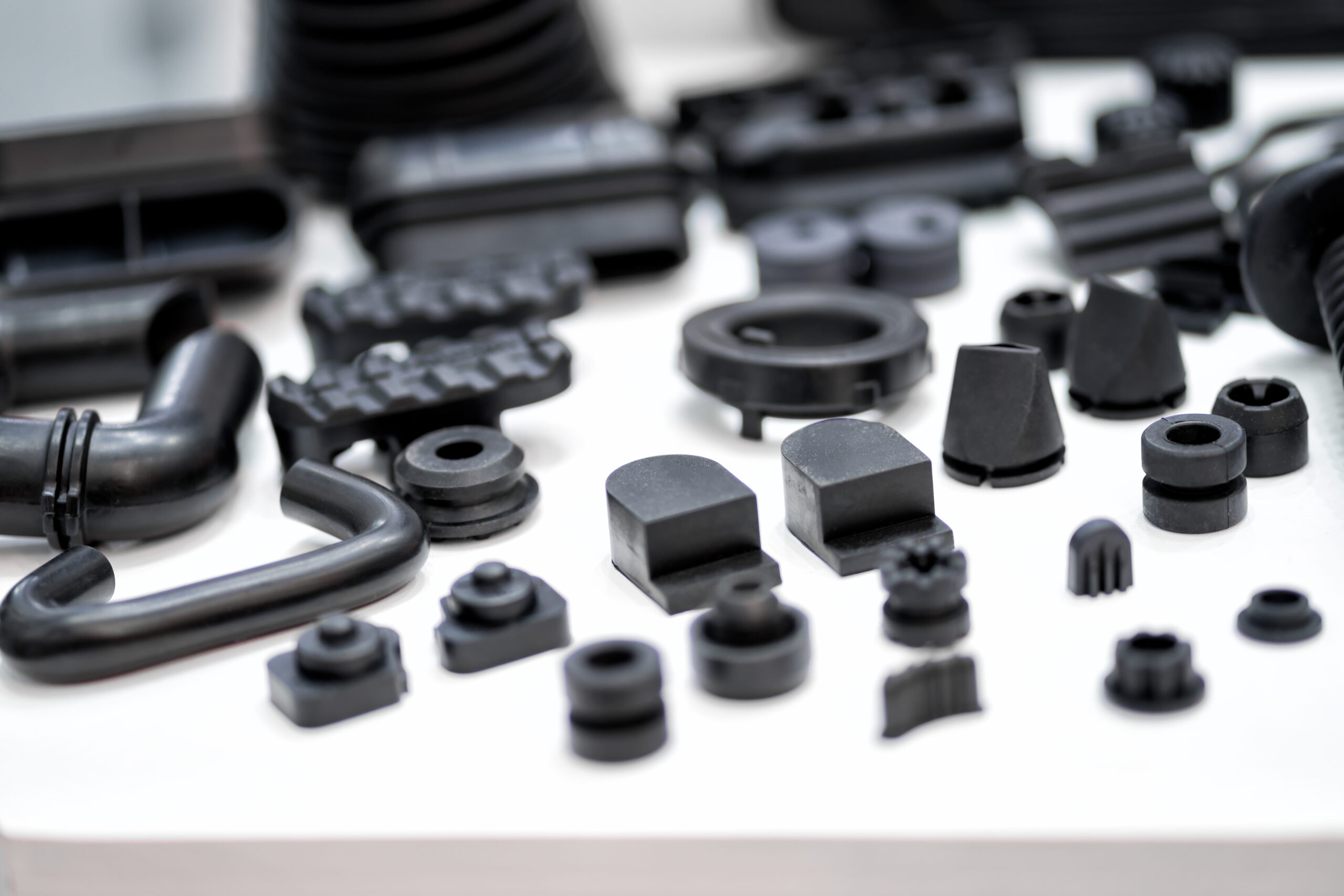
META-aiviCase Study
Injection Molding Machine Monitoring Using IP Cams
Customer
The customer is an international manufacturer of plastics for the automotive industry.
Case
Automating Injection Molding Machine Malfunction Detection
In optimizing plastic injection molding precision, a solution was required by the customer to establish a reliable and streamlined automated detection system. Previously reliant on manual oversight, the original process risked downtime and high maintenance costs. Our solution automates the detection, signaling the machine to avoid closing and initiating a new mold if the pin is extended. This shift from manual to automated detection enhances operational efficiency, minimizing downtime and improving production reliability.
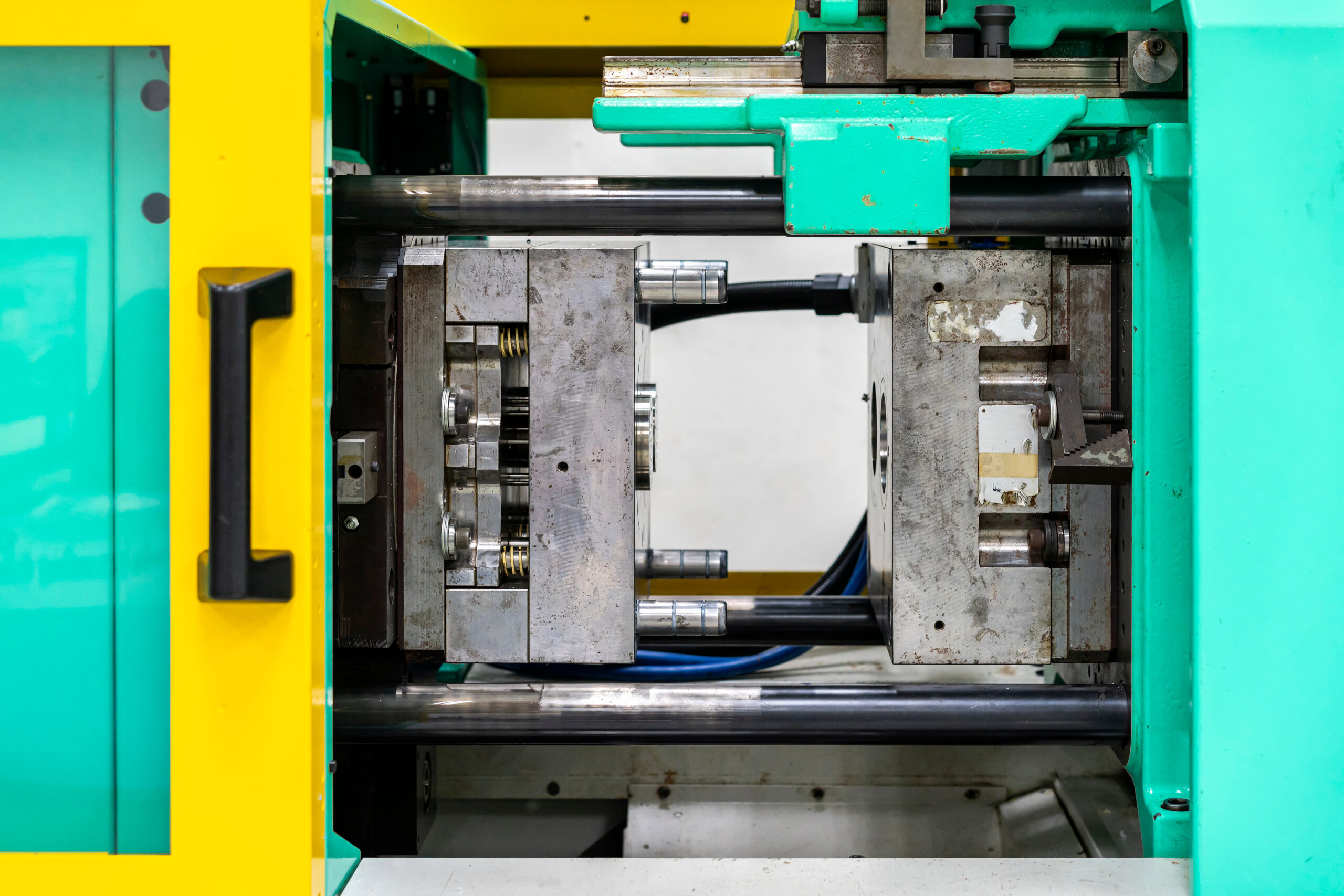
Challenge
Machine Connectivity and Control System Integration
The customer faced challenges due to the plastic injection molding machine’s lack of smart connectivity. This impeded the implementation of an automated ejector pin detection system, compromising real-time communication and data transfer efficiency. Also, the absence of an integrated control system complicated the detection solution’s integration, risking machine malfunctions, frequent maintenance, and disruptive production downtime.
Solution
Machine Malfunction Detection Using IP Cameras
To overcome connectivity and control challenges, we implemented an innovative solution using META-aivi AI image recognition paired with an IP camera to detect mold closure in real-time. In the event of the ejector pin’s failure to retract, the system issues an instant notification and pauses the machine ensuring operational safety and minimizing disruptions. This streamlined solution not only automates malfunction detection but also enhances production efficiency by reducing the need for manual oversight and preventing unplanned downtime.