Quelles sont les différences entre l’IA et l’AOI ?
Introduction à l’AOI
La transition d’une époque de fabrication caractérisée par la production de masse avec une variété limitée à un modèle dynamique d’aujourd’hui mettant l’accent sur la production de biens à faible volume et à grande variété a rendu le contrôle de qualité et l’inspection plus complexes et difficiles. Les produits sont désormais disponibles dans une plus large gamme de formes, tailles, matériaux et autres caractéristiques, entraînant souvent des défauts moins définis.
En conséquence, les systèmes AOI (Inspection Optique Automatisée) sont devenus la solution prédominante pour la détection des défauts dans les processus industriels. Cependant, l’AOI conventionnel dépend d’échantillons de défauts prédéfinis et de paramètres fixes pour la détection des défauts, ce qui limite la capacité des systèmes AOI à effectuer des inspections agiles et rapides. La probabilité que les systèmes d’inspection traditionnels passent à côté des défauts augmente considérablement ; cependant, l’IA offre une solution transformante pour la vision machine en facilitant des inspections plus flexibles et plus efficaces.
En conséquence, les systèmes AOI (Inspection Optique Automatisée) sont devenus la solution prédominante pour la détection des défauts dans les processus industriels. Cependant, l’AOI conventionnel dépend d’échantillons de défauts prédéfinis et de paramètres fixes pour la détection des défauts, ce qui limite la capacité des systèmes AOI à effectuer des inspections agiles et rapides. La probabilité que les systèmes d’inspection traditionnels passent à côté des défauts augmente considérablement ; cependant, l’IA offre une solution transformante pour la vision machine en facilitant des inspections plus flexibles et plus efficaces.
Détection des défauts avec l’AOI
À mesure que les produits électroniques grand public continuent de progresser, des secteurs comme les semi-conducteurs, l’optoélectronique et la fabrication intelligente connaissent une croissance substantielle. Avec des défauts susceptibles d’affecter la fonctionnalité des produits, la demande d’un meilleur rendement dans les secteurs de la fabrication est de plus en plus forte. Les lignes de production traditionnelles se sont appuyées sur l’inspection manuelle des motifs de défauts des produits, mais cette méthode ne permet pas de répondre à la demande d’une inspection minutieuse et d’une efficacité de production accrue.
Les systèmes AOI, alimentés par la technologie de vision machine, combinent harmonieusement optique, contrôle électronique, mécanique et logiciels d’inspection pour effectuer des tâches d’inspection précises. Ces systèmes améliorent l’efficacité de la détection des défauts en mettant en évidence les caractéristiques des images grâce à des configurations optimisées de la source lumineuse et en utilisant des techniques avancées de traitement d’image par ordinateur pour un positionnement et une inspection précis. En scannant rapidement les défauts, les contaminants et les irrégularités des produits finis et semi-finis sur la ligne de production, l’AOI peut grandement améliorer les mesures de contrôle de la qualité.
Comparés aux méthodes d’inspection manuelles, les systèmes AOI offrent un niveau de cohérence supérieur dans la détection des défauts. De plus, les systèmes AOI équipés de caméras haute résolution peuvent discerner des détails fins qui peuvent être difficiles à détecter à l’œil humain. Leur capacité à inspecter des milliers d’articles par minute permet également de résoudre les inefficacités inhérentes aux processus d’inspection visuelle manuelle traditionnels.
Les systèmes AOI, alimentés par la technologie de vision machine, combinent harmonieusement optique, contrôle électronique, mécanique et logiciels d’inspection pour effectuer des tâches d’inspection précises. Ces systèmes améliorent l’efficacité de la détection des défauts en mettant en évidence les caractéristiques des images grâce à des configurations optimisées de la source lumineuse et en utilisant des techniques avancées de traitement d’image par ordinateur pour un positionnement et une inspection précis. En scannant rapidement les défauts, les contaminants et les irrégularités des produits finis et semi-finis sur la ligne de production, l’AOI peut grandement améliorer les mesures de contrôle de la qualité.
Comparés aux méthodes d’inspection manuelles, les systèmes AOI offrent un niveau de cohérence supérieur dans la détection des défauts. De plus, les systèmes AOI équipés de caméras haute résolution peuvent discerner des détails fins qui peuvent être difficiles à détecter à l’œil humain. Leur capacité à inspecter des milliers d’articles par minute permet également de résoudre les inefficacités inhérentes aux processus d’inspection visuelle manuelle traditionnels.
Applications industrielles de l’AOI
La technologie AOI est largement utilisée dans divers secteurs industriels pour inspecter les produits en quête de déformations, de dommages, de composants manquants, de salissures, de rayures et d’autres défauts, tout en effectuant des tâches critiques telles que la lecture de codes-barres, les mesures précises et l’inspection de l’impression. En conséquence, de nombreux secteurs, notamment l’électronique, le textile, l’alimentation et la boisson et l’automobile, bénéficient de la technologie AOI.
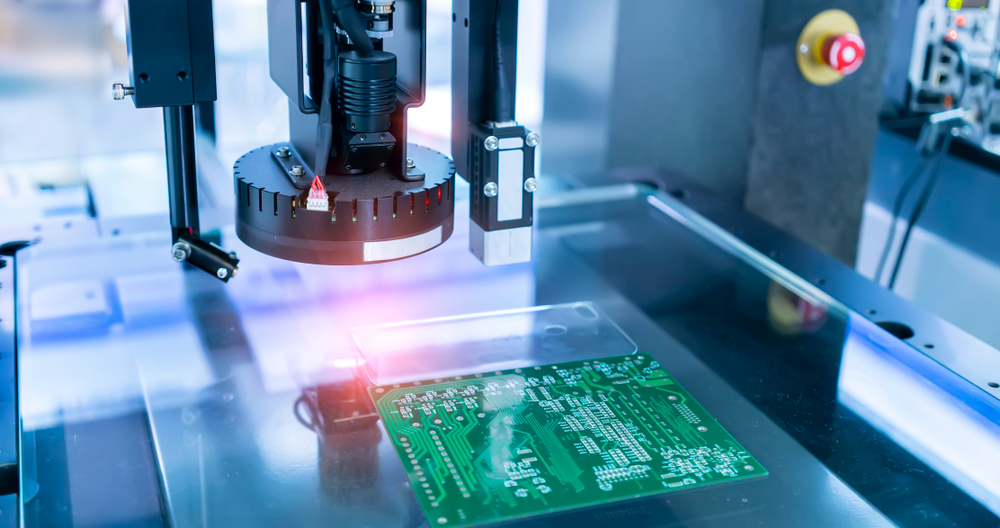
Limites de l’AOI pour la détection des défauts
Bien que l’adoption de l’AOI soit devenue courante dans divers secteurs industriels, la nature hautement personnalisée de l’AOI présente des défis et des limitations à sa mise en œuvre généralisée. En particulier, lorsqu’il s’agit de défauts de produits complexes, d’arrière-plans d’image et de variations d’éclairage, les systèmes AOI peuvent rencontrer des contraintes.
L’AOI fonctionne sur un mécanisme de jugement basé sur des règles où la logique de détection est programmée dans le système. L’AOI ne peut identifier des défauts qu’en fonction de paramètres prédéfinis établis comme référence pour l’inspection des défauts échantillons. Par exemple, si la logique de détection définit des défauts comme étant circulaires, tout défaut non circulaire peut passer inaperçu pour le système AOI. Des types de défauts générés de manière aléatoire, tels que des variations de qualité de coquille d’œuf, des défauts anormaux dans l’assemblage PCBA, des taches d’huile sur des boucles en plastique ou des rayures sur des pièces métalliques estampées, posent des défis importants pour que l’AOI détecte efficacement de telles complexités.
Pour réduire le risque de défauts manqués, les systèmes AOI sont souvent réglés sur des paramètres avec un niveau strict, ce qui rend l’AOI excessivement sensible et susceptible aux faux positifs. De plus, les opérateurs du système doivent constamment affiner les algorithmes et les paramètres du système, tandis que les lignes de production peuvent nécessiter des inspections répétées des produits pour éviter l’oubli de défauts ou les faux positifs. Ces facteurs ont un impact significatif sur l’efficacité de la production et augmentent les coûts de production.
L’efficacité de l’AOI dépend de la coordination précise des sources lumineuses, des caméras et des objectifs. En ce qui concerne les sources lumineuses, l’ajustement de leur intensité et de leurs caractéristiques est crucial pour améliorer le contraste et afficher efficacement les caractéristiques des objets. Cet ajustement doit être personnalisé en fonction du matériau, de la couleur et de la forme de l’objet à inspecter pour obtenir des images optimales et réduire le risque de faux positifs. Lors de la sélection des caméras, des facteurs tels que les composants de sensibilité, la résolution et les taux de trame doivent être soigneusement pris en compte en fonction des exigences de l’inspection. Ces caméras doivent être associées à des objectifs appropriés pour exploiter pleinement les capacités du système optique.
En plus des complexités des détails des équipements affectant l’imagerie, les opérateurs doivent également gérer la tâche de reconfigurer les paramètres de la machine et l’alignement lorsqu’il y a des ajustements ou des remplacements de composants nécessaires, en s’appuyant sur leur expérience. De plus, l’ajustement des composants matériels et logiciels est intrinsèquement complexe, et les temps de réparation peuvent varier considérablement, allant de quelques jours à plusieurs mois. Cela présente des défis pour répondre aux exigences dynamiques des lignes de production modernes. En conséquence, de nombreuses industries utilisant l’AOI ont récemment adopté l’intelligence artificielle (IA) pour améliorer l’exactitude et l’efficacité de l’inspection.
L’AOI fonctionne sur un mécanisme de jugement basé sur des règles où la logique de détection est programmée dans le système. L’AOI ne peut identifier des défauts qu’en fonction de paramètres prédéfinis établis comme référence pour l’inspection des défauts échantillons. Par exemple, si la logique de détection définit des défauts comme étant circulaires, tout défaut non circulaire peut passer inaperçu pour le système AOI. Des types de défauts générés de manière aléatoire, tels que des variations de qualité de coquille d’œuf, des défauts anormaux dans l’assemblage PCBA, des taches d’huile sur des boucles en plastique ou des rayures sur des pièces métalliques estampées, posent des défis importants pour que l’AOI détecte efficacement de telles complexités.
Pour réduire le risque de défauts manqués, les systèmes AOI sont souvent réglés sur des paramètres avec un niveau strict, ce qui rend l’AOI excessivement sensible et susceptible aux faux positifs. De plus, les opérateurs du système doivent constamment affiner les algorithmes et les paramètres du système, tandis que les lignes de production peuvent nécessiter des inspections répétées des produits pour éviter l’oubli de défauts ou les faux positifs. Ces facteurs ont un impact significatif sur l’efficacité de la production et augmentent les coûts de production.
L’efficacité de l’AOI dépend de la coordination précise des sources lumineuses, des caméras et des objectifs. En ce qui concerne les sources lumineuses, l’ajustement de leur intensité et de leurs caractéristiques est crucial pour améliorer le contraste et afficher efficacement les caractéristiques des objets. Cet ajustement doit être personnalisé en fonction du matériau, de la couleur et de la forme de l’objet à inspecter pour obtenir des images optimales et réduire le risque de faux positifs. Lors de la sélection des caméras, des facteurs tels que les composants de sensibilité, la résolution et les taux de trame doivent être soigneusement pris en compte en fonction des exigences de l’inspection. Ces caméras doivent être associées à des objectifs appropriés pour exploiter pleinement les capacités du système optique.
En plus des complexités des détails des équipements affectant l’imagerie, les opérateurs doivent également gérer la tâche de reconfigurer les paramètres de la machine et l’alignement lorsqu’il y a des ajustements ou des remplacements de composants nécessaires, en s’appuyant sur leur expérience. De plus, l’ajustement des composants matériels et logiciels est intrinsèquement complexe, et les temps de réparation peuvent varier considérablement, allant de quelques jours à plusieurs mois. Cela présente des défis pour répondre aux exigences dynamiques des lignes de production modernes. En conséquence, de nombreuses industries utilisant l’AOI ont récemment adopté l’intelligence artificielle (IA) pour améliorer l’exactitude et l’efficacité de l’inspection.
Détection des défauts avec l’IA
La principale différence entre l’inspection basée sur l’IA et la détection des défauts traditionnelle par AOI réside dans leur dépendance aux règles empiriques. L’IA fonctionne comme un nouvel apprenti, capable d’imiter dans une certaine mesure les capacités d’inspection d’un maître artisan. L’IA peut définir de manière autonome les plages de défauts et les modèles de détection anormaux en utilisant de grandes quantités de données valides et en entraînant le modèle du système à l’aide de techniques d’apprentissage profond. L’IA peut automatiquement identifier les paramètres optimaux pour les défauts acceptables (OK) et non acceptables (NG). Cela permet une détection efficace des défauts inconnus, garantit la cohérence des normes d’inspection et améliore considérablement la précision de l’inspection.
En raison des variations importantes des connaissances de domaine entre les secteurs, les ingénieurs AOI traditionnels impliqués dans le développement des systèmes AOI pour des secteurs spécifiques peuvent rencontrer des difficultés à résoudre rapidement les problèmes pratiques sur le terrain. Par conséquent, des solutions efficaces nécessitent souvent une collaboration avec des experts du secteur pour concevoir du matériel et des règles AOI adaptés aux besoins de l’industrie. En revanche, les systèmes de détection des défauts basés sur l’IA apprennent les caractéristiques d’image nécessaires pour la détection via des interfaces. Une fois formés, les systèmes IA peuvent générer de manière autonome des règles de détection. Il existe des différences notables en termes d’efficacité d’apprentissage et de puissance d’exécution entre ces deux approches.
En plus d’optimiser la précision de la détection grâce à l’apprentissage profond, la technologie IA aborde de manière significative les problèmes liés à l’impact des sources lumineuses sur les performances de détection. Les systèmes AOI traditionnels sont souvent limités par les conditions d’éclairage, les angles de prise de vue, les ombres, les réflexions et le matériau et la forme de l’objet inspecté (en particulier les matériaux semi-transparents et les surfaces métalliques). Ces limitations entravent fréquemment l’obtention de résultats de détection précis. En revanche, la précision de l’inspection basée sur l’IA dépend moins des sources lumineuses. Avec une source lumineuse stable, l’IA peut effectuer efficacement la détection et la classification des défauts même dans des scénarios avec des contours flous, des formes différentes et des interférences provenant de matériaux métalliques réfléchissants.
La détection des défauts par IA excelle dans les défauts de surface et d’apparence complexes, tels que les bosses et les rayures sur des objets réfléchissants. De plus, l’IA peut être compétente dans les tâches de reconnaissance optique de caractères (OCR), même lorsqu’il s’agit d’inspecter des caractères déformés ou moins reconnaissables. En outre, les systèmes basés sur l’IA sont capables de filtrer les motifs et défauts imprévisibles, indépendamment des variations de couleur et de taille, des déformations importantes, des formes complexes ou de la dispersion aléatoire. L’IA analyse les données de manière exhaustive, déterminant avec précision la présence de défauts.
Les systèmes de vision par IA surpassent donc les systèmes AOI traditionnels basés sur des règles en termes de vitesse, de précision et de coûts de main-d’œuvre, en relevant les défis inhérents aux applications complexes de détection et de classification.
En raison des variations importantes des connaissances de domaine entre les secteurs, les ingénieurs AOI traditionnels impliqués dans le développement des systèmes AOI pour des secteurs spécifiques peuvent rencontrer des difficultés à résoudre rapidement les problèmes pratiques sur le terrain. Par conséquent, des solutions efficaces nécessitent souvent une collaboration avec des experts du secteur pour concevoir du matériel et des règles AOI adaptés aux besoins de l’industrie. En revanche, les systèmes de détection des défauts basés sur l’IA apprennent les caractéristiques d’image nécessaires pour la détection via des interfaces. Une fois formés, les systèmes IA peuvent générer de manière autonome des règles de détection. Il existe des différences notables en termes d’efficacité d’apprentissage et de puissance d’exécution entre ces deux approches.
En plus d’optimiser la précision de la détection grâce à l’apprentissage profond, la technologie IA aborde de manière significative les problèmes liés à l’impact des sources lumineuses sur les performances de détection. Les systèmes AOI traditionnels sont souvent limités par les conditions d’éclairage, les angles de prise de vue, les ombres, les réflexions et le matériau et la forme de l’objet inspecté (en particulier les matériaux semi-transparents et les surfaces métalliques). Ces limitations entravent fréquemment l’obtention de résultats de détection précis. En revanche, la précision de l’inspection basée sur l’IA dépend moins des sources lumineuses. Avec une source lumineuse stable, l’IA peut effectuer efficacement la détection et la classification des défauts même dans des scénarios avec des contours flous, des formes différentes et des interférences provenant de matériaux métalliques réfléchissants.
La détection des défauts par IA excelle dans les défauts de surface et d’apparence complexes, tels que les bosses et les rayures sur des objets réfléchissants. De plus, l’IA peut être compétente dans les tâches de reconnaissance optique de caractères (OCR), même lorsqu’il s’agit d’inspecter des caractères déformés ou moins reconnaissables. En outre, les systèmes basés sur l’IA sont capables de filtrer les motifs et défauts imprévisibles, indépendamment des variations de couleur et de taille, des déformations importantes, des formes complexes ou de la dispersion aléatoire. L’IA analyse les données de manière exhaustive, déterminant avec précision la présence de défauts.
Les systèmes de vision par IA surpassent donc les systèmes AOI traditionnels basés sur des règles en termes de vitesse, de précision et de coûts de main-d’œuvre, en relevant les défis inhérents aux applications complexes de détection et de classification.
Cas d’étude de détection des défauts par IA
Dans l’industrie pharmaceutique, les lignes de production de blisters manipulent généralement entre 5 000 et 40 000 pilules par heure. Cependant, des erreurs peuvent survenir lors du remplissage, entraînant des défauts tels que des blisters vides, des contenus de mauvaise qualité ou des éclaboussures de poudre provenant des gélules. En formant des modèles d’IA dans SolVision avec une variété d’images de défauts, chaque pack et condition de remplissage peut être rapidement et précisément identifié, étiqueté et classé.