Guida completa al prelievo casuale da contenitori (Random Bin Picking)
Che cos’è il prelievo casuale da contenitori (Random Bin Picking)?
Il prelievo casuale da contenitori (Random Bin Picking) è un compito di automazione robotica in cui un robot, assistito da una telecamera 3D, preleva oggetti disposti in modo casuale, con orientamenti sconosciuti e posizioni non strutturate, da un contenitore o cassa. Questo processo viene generalmente implementato in ambienti di produzione e magazzino, con l’obiettivo principale di automatizzare il recupero di articoli da pile disordinate o non strutturate.
Settori e esempi di applicazione del prelievo casuale da contenitori (Random Bin Picking)
Il prelievo casuale da contenitori è estremamente prezioso nei settori in cui la movimentazione e la selezione di oggetti da contenitori o casse è ripetitiva, richiede molta manodopera ed è dispendiosa in termini di tempo. Di seguito sono riportati alcuni esempi di applicazione del bin picking in diversi settori.
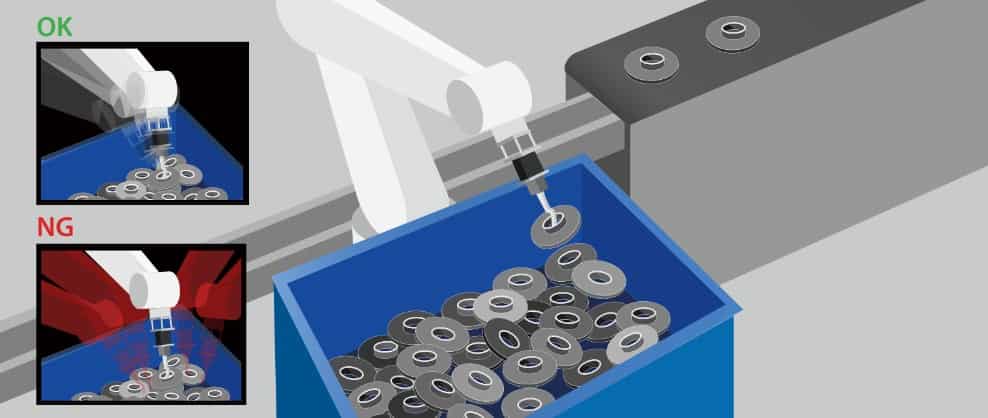
Prelievo casuale da contenitori di oggetti metallici
Logistica
Nel settore della logistica e della gestione dei magazzini, il prelievo casuale da contenitori viene utilizzato per ordinare e movimentare numerosi pacchi disposti in modo casuale all’interno di contenitori. Ad esempio, in un progetto per una piattaforma globale di e-commerce, pacchi assortiti venivano prelevati dai contenitori e posizionati su un nastro trasportatore ad alta velocità. La sfida principale era mantenere elevati ritmi di prelievo gestendo in sicurezza pacchi pesanti, evitando errori o danni nella movimentazione. La soluzione IA di Solomon ha permesso al sistema di operare rapidamente, soddisfacendo le esigenze di elevata produttività e garantendo al contempo un manipolamento accurato e sicuro di pacchi di dimensioni e peso variabili.
Automotive
Nel settore automotive, il prelievo casuale da contenitori viene utilizzato per gestire e ordinare componenti automobilistici. La principale sfida per i sistemi di bin picking è ottenere un’elevata precisione, assicurando che ogni parte sia correttamente classificata, prelevata e impilata nel modo giusto. In un progetto per un importante costruttore automobilistico giapponese, AccuPick è stato impiegato per gestire con precisione i componenti auto, evitando errori e difetti nell’assemblaggio e nel posizionamento, migliorando così l’efficienza complessiva.
Alimentare e bevande
Nel settore alimentare, il prelievo casuale da contenitori svolge un ruolo cruciale nell’automazione della selezione e movimentazione dei prodotti alimentari, migliorando significativamente l’efficienza operativa. Uno dei progetti più rilevanti di Solomon in questo ambito ha visto la collaborazione con una multinazionale leader nel settore dolciario per il prelievo di biscotti confezionati da contenitori e il loro trasferimento su un nastro trasportatore. La sfida principale era il tempo ciclo, poiché il sistema doveva prelevare e posizionare circa 30–35 biscotti al minuto. L’automazione è stata implementata per ridurre lo sforzo fisico degli operatori, minimizzando così il rischio di infortuni muscoloscheletrici e migliorando sia la sicurezza sul lavoro sia l’efficienza della linea di produzione.
Manifatturiero
Il bin picking è ampiamente utilizzato nel settore manifatturiero per il prelievo e la selezione di vari componenti. Un importante produttore di robot industriali e macchinari per l’automazione necessitava di un sistema di bin picking casuale ad alta velocità per oggetti metallici specifici. Le principali sfide erano i rigorosi requisiti di tempo ciclo e di precisione. Gli oggetti dovevano essere impilati correttamente nella stazione di rilascio, e qualsiasi errore nella precisione di prelievo avrebbe comportato un impilamento errato. Gli articoli potevano essere posizionati con visuale dall’alto o posteriore e con angoli di inclinazione variabili, il che richiedeva all’IA di rilevare con precisione ciascun lato e il relativo angolo per un posizionamento accurato. La superficie lucida degli oggetti metallici rappresentava un’ulteriore sfida per le telecamere 3D, poiché i riflessi della luce potevano distorcere sia l’immagine 2D sia la nuvola di punti 3D, riducendo la precisione del prelievo. Per superare questo problema, è stata utilizzata una telecamera industriale 3D SolScan dotata di proiettore a luce verde anziché la tradizionale luce bianca.
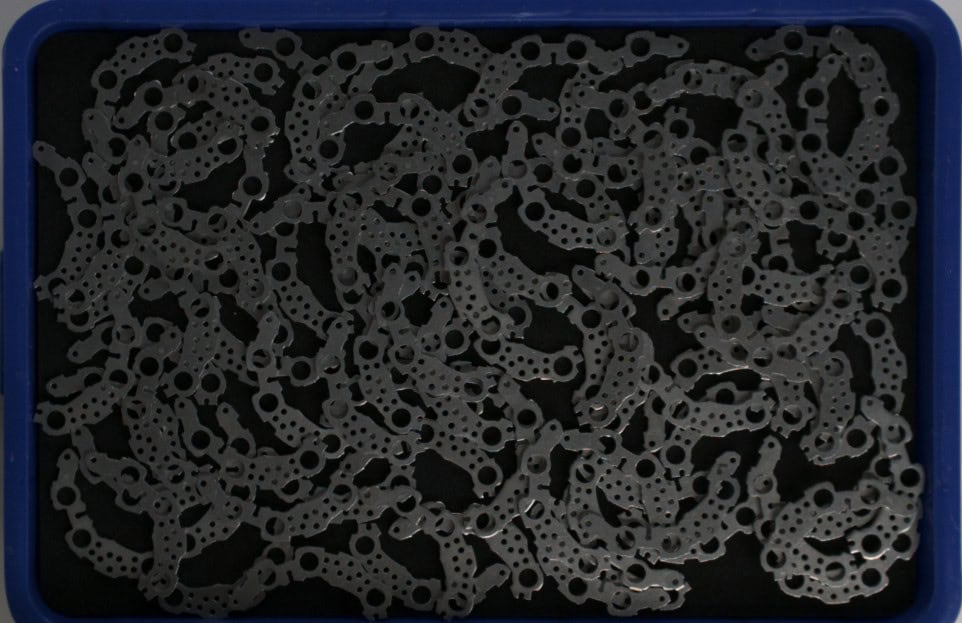
Immagine 2D originale
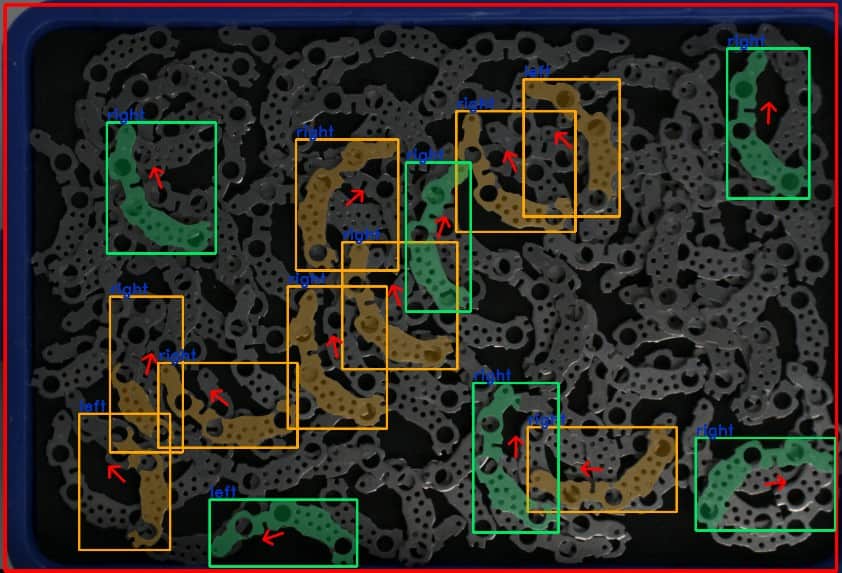
Rilevamento 2D con IA e riconoscimento dell’angolo di inclinazione
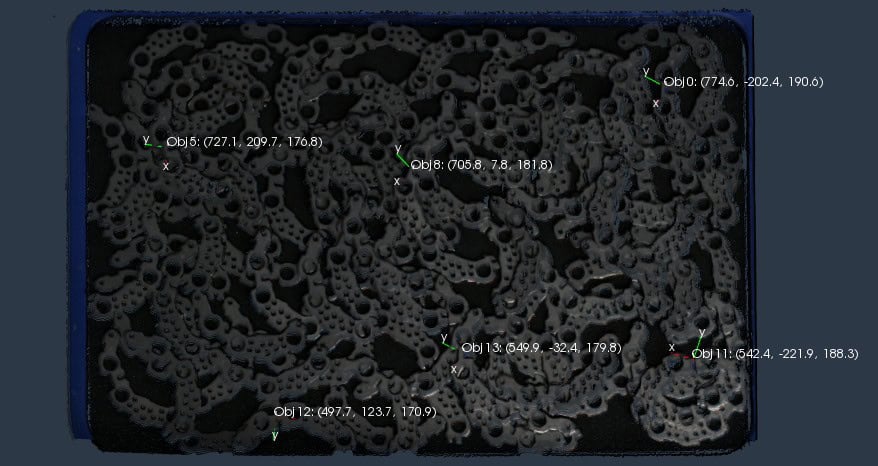
Nuvola di punti 3D con posizionamento dei punti di prelievo
Farmaceutico e medico
Nel settore farmaceutico e medico, i sistemi di bin picking sono fondamentali per la gestione di articoli diversi in ambienti ad alta velocità, dove la precisione è cruciale. In questo caso, un distributore farmaceutico gestiva vari contenitori, inclusi scatole e flaconi di diverse forme, dimensioni e colori, con circa cinque oggetti per contenitore disposti in posizioni e orientamenti casuali. La sfida principale era garantire che il codice a barre del prodotto rimanesse visibile durante il prelievo, poiché gli articoli dovevano essere posizionati tra i lettori di codici a barre per la scansione. L’area di lavoro era limitata e i robot dovevano operare ad alta velocità per rispettare i tempi ciclo richiesti, aumentando il rischio di collisioni. Per affrontare questa sfida è stato utilizzato AccuPick. Il suo software di pianificazione del movimento ha calcolato traiettorie sicure e prive di collisioni, mentre l’IA integrata ha consentito un rilevamento ad alta precisione, permettendo al robot di prelevare oggetti da qualsiasi posizione (dall’alto, dal lato o dal basso) senza coprire il codice a barre. Sono stati impiegati due diversi organi di presa robotici: uno con una grande ventosa e l’altro con una ventosa più piccola. In base ai risultati del rilevamento degli oggetti, alla posizione e al tipo (scatola o flacone), sono state stabilite condizioni e regole strategiche per garantire la selezione dell’organo di presa più adatto a ciascun caso specifico.
Elementi essenziali di un sistema di prelievo casuale da contenitori (Random Bin Picking)
Calibrazione del punto centrale dell’utensile (Tool Center Point, TCP)
La calibrazione del TCP (Tool Center Point) del robot deve essere eseguita una volta selezionato e montato l’organo di presa (end-effector) sulla flangia del robot. Il TCP funge da punto di riferimento per indicare al robot la posizione e l’orientamento precisi dell’organo di presa.
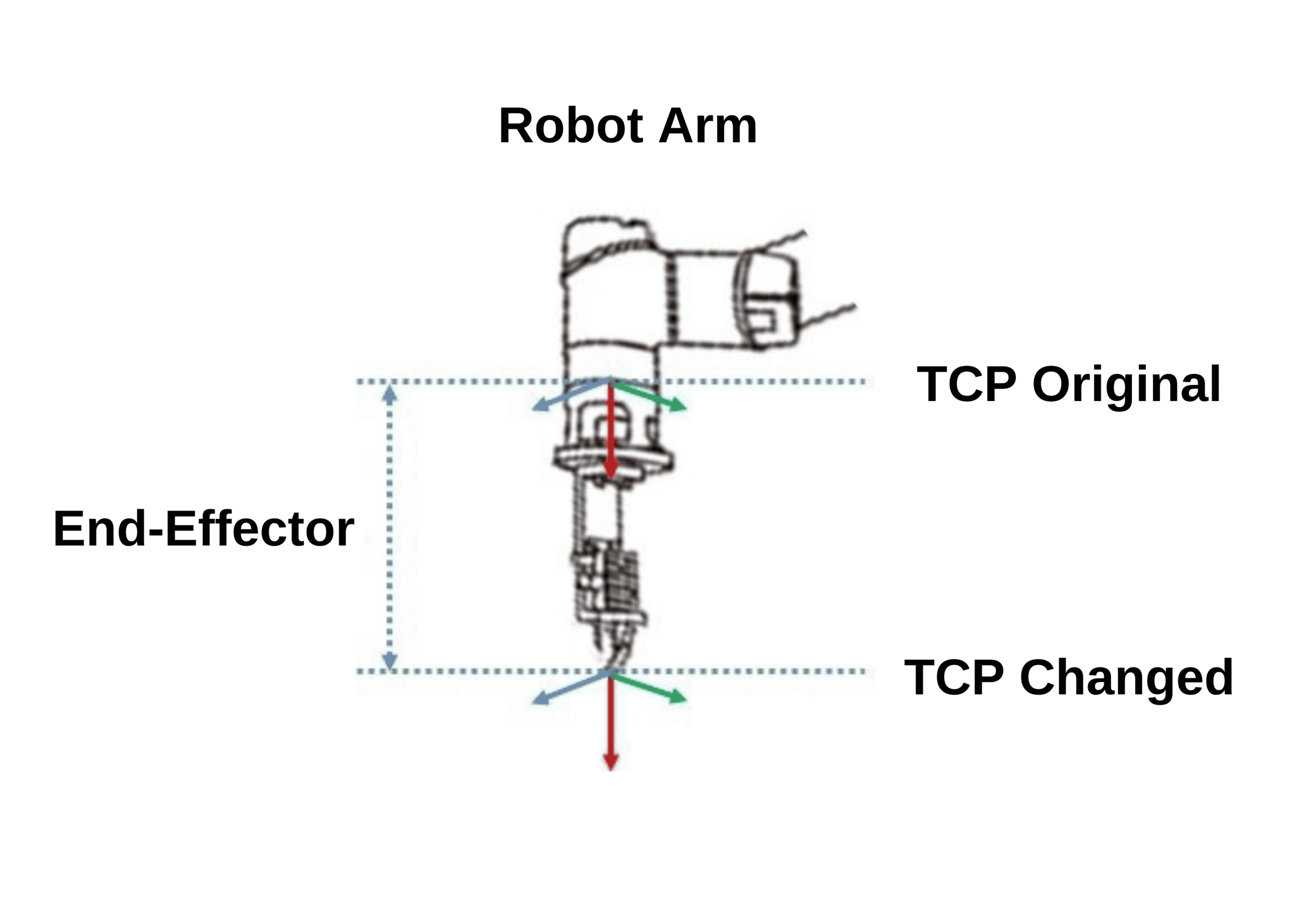
Calibrazione del TCP (Tool Center Point)
Calibrazione tra sistema di visione e robot
La calibrazione tra il sistema di visione e il robot è essenziale. Poiché la telecamera 3D ha il proprio punto di origine delle coordinate alla base della telecamera, mentre il robot ha il proprio punto di origine alla base del braccio robotico, la calibrazione consente al robot di comprendere il sistema di coordinate della telecamera e convertire tali coordinate nel proprio sistema di riferimento. Di conseguenza, qualsiasi coordinata di posizione e rotazione inviata dallo scanner 3D al robot sarà interpretata con precisione, permettendo al robot di raggiungere il punto specifico con la posizione e l’orientamento richiesti.
Scansione 3D e rilevamento degli oggetti
Lo scanner 3D acquisisce sia immagini 2D sia nuvole di punti 3D degli oggetti presenti nel contenitore. Questi dati vengono utilizzati per generare un punto di prelievo per gli oggetti che soddisfano i criteri base per il prelievo. Tali criteri possono variare in base al progetto, ma in genere includono:
• Oggetti posizionati sulla superficie superiore del contenitore.
• Oggetti non occlusi o solo parzialmente occlusi da altri articoli.
• Caratteristiche visibili che aiutano a determinare l’orientamento corretto per il prelievo.
• Oggetti posizionati e orientati in modo sicuro per evitare collisioni del robot o del suo end-effector durante il prelievo.
• Oggetti posizionati sulla superficie superiore del contenitore.
• Oggetti non occlusi o solo parzialmente occlusi da altri articoli.
• Caratteristiche visibili che aiutano a determinare l’orientamento corretto per il prelievo.
• Oggetti posizionati e orientati in modo sicuro per evitare collisioni del robot o del suo end-effector durante il prelievo.
Generazione ed esecuzione del punto di prelievo (Pick-Point)
Il punto di prelievo (pick-point) per ciascun oggetto include generalmente sia le coordinate di posizione sia quelle di rotazione. Una volta generato, il robot riceve il pick-point e il suo controllore calcola la traiettoria per raggiungerlo. Per applicazioni più complesse in ambienti che richiedono l’evitamento delle collisioni, è necessario l’utilizzo di un software di pianificazione del movimento per calcolare una traiettoria sicura. Raggiunto il pick-point, il robot preleva l’oggetto e lo deposita nella posizione o nel contenitore desiderato.
Ripetizione del ciclo
Una volta che tutti gli oggetti rilevati nel ciclo corrente sono stati prelevati e depositati, inizia un nuovo ciclo a partire dalla fase di scansione. Questo garantisce un’operazione continua fino allo svuotamento completo del contenitore.
Sfide e soluzioni del prelievo casuale da contenitori (Random Bin Picking)
Requisiti rigorosi di tempo ciclo
I progetti con requisiti rigorosi di tempo ciclo affrontano sfide significative, poiché ogni fase deve essere completata rapidamente per raggiungere gli obiettivi complessivi. Le principali considerazioni includono:
• Tempo di acquisizione della telecamera 3D: la telecamera 3D deve acquisire rapidamente sia immagini 2D sia nuvole di punti 3D.
• Generazione di immagini e nuvole di punti: gli algoritmi per la generazione di immagini 2D e nuvole di punti 3D devono essere efficienti e ottimizzati.
• Identificazione degli oggetti: l’algoritmo di identificazione degli oggetti deve essere veloce; l’impiego dell’IA può aumentare significativamente velocità e precisione.
• Posizionamento del punto di prelievo: l’algoritmo per determinare i punti di prelievo deve essere rapido; anche in questo caso l’IA può contribuire a ottenere alte prestazioni.
• Pianificazione del movimento: il sistema di motion planning deve calcolare rapidamente traiettorie sicure.
• Velocità del robot: il robot deve operare ad alta velocità per rispettare i tempi ciclo richiesti.
• Selezione dell’end-effector: la scelta dell’organo di presa appropriato è cruciale per ridurre i fallimenti nel prelievo e garantire la stabilità dell’oggetto durante i movimenti robotici.
• Tempo di acquisizione della telecamera 3D: la telecamera 3D deve acquisire rapidamente sia immagini 2D sia nuvole di punti 3D.
• Generazione di immagini e nuvole di punti: gli algoritmi per la generazione di immagini 2D e nuvole di punti 3D devono essere efficienti e ottimizzati.
• Identificazione degli oggetti: l’algoritmo di identificazione degli oggetti deve essere veloce; l’impiego dell’IA può aumentare significativamente velocità e precisione.
• Posizionamento del punto di prelievo: l’algoritmo per determinare i punti di prelievo deve essere rapido; anche in questo caso l’IA può contribuire a ottenere alte prestazioni.
• Pianificazione del movimento: il sistema di motion planning deve calcolare rapidamente traiettorie sicure.
• Velocità del robot: il robot deve operare ad alta velocità per rispettare i tempi ciclo richiesti.
• Selezione dell’end-effector: la scelta dell’organo di presa appropriato è cruciale per ridurre i fallimenti nel prelievo e garantire la stabilità dell’oggetto durante i movimenti robotici.
Elevata precisione di prelievo
Raggiungere un’elevata precisione di prelievo è fondamentale per un bin picking efficace. Le considerazioni chiave includono:
• Scanner 3D appropriato: è essenziale selezionare uno scanner 3D adatto al materiale dell’oggetto, alla distanza operativa e alle dimensioni del contenitore.
• Alta risoluzione: lo scanner 3D deve offrire una risoluzione elevata per una cattura dettagliata.
• Visione artificiale e pre-elaborazione dell’immagine: l’utilizzo di tecniche avanzate di visione artificiale e di pre-elaborazione delle immagini può migliorare significativamente la precisione.
• IA per il rilevamento degli oggetti: la scelta dell’algoritmo IA corretto può aumentare la precisione nel riconoscimento degli oggetti.
• IA per il posizionamento del punto di prelievo: i metodi di 3D matching basati su IA possono affinare ulteriormente la precisione nel posizionamento del pick-point.
• Ottimizzazione avanzata: una messa a punto completa dei parametri dello scanner 3D, delle tecniche di pre-elaborazione delle immagini, dell’algoritmo IA di rilevamento 2D e del metodo di 3D matching per il posizionamento è fondamentale per ottenere prestazioni ottimali.
• Ambiente di illuminazione stabile: garantire un’illuminazione stabile è importante per ottenere risultati coerenti.
• Scanner 3D appropriato: è essenziale selezionare uno scanner 3D adatto al materiale dell’oggetto, alla distanza operativa e alle dimensioni del contenitore.
• Alta risoluzione: lo scanner 3D deve offrire una risoluzione elevata per una cattura dettagliata.
• Visione artificiale e pre-elaborazione dell’immagine: l’utilizzo di tecniche avanzate di visione artificiale e di pre-elaborazione delle immagini può migliorare significativamente la precisione.
• IA per il rilevamento degli oggetti: la scelta dell’algoritmo IA corretto può aumentare la precisione nel riconoscimento degli oggetti.
• IA per il posizionamento del punto di prelievo: i metodi di 3D matching basati su IA possono affinare ulteriormente la precisione nel posizionamento del pick-point.
• Ottimizzazione avanzata: una messa a punto completa dei parametri dello scanner 3D, delle tecniche di pre-elaborazione delle immagini, dell’algoritmo IA di rilevamento 2D e del metodo di 3D matching per il posizionamento è fondamentale per ottenere prestazioni ottimali.
• Ambiente di illuminazione stabile: garantire un’illuminazione stabile è importante per ottenere risultati coerenti.
Orientamento casuale degli oggetti
Gli oggetti nei contenitori spesso si trovano in disposizioni casuali, con orientamenti sconosciuti e posizioni non strutturate. Questa casualità può causare interferenze tra gli oggetti stessi. Per superare queste sfide, è possibile adottare diverse strategie:
• Approccio strato per strato: scansionare e prelevare gli oggetti più adatti, quindi effettuare una nuova scansione per avviare l’iterazione successiva, procedendo strato dopo strato.
• Agitatore per contenitori (Bin Shaker): utilizzare un agitatore per modificare la posizione degli oggetti all’interno del contenitore.
• Prelievo a due fasi: prelevare inizialmente l’oggetto nel modo più efficace possibile, per poi separarlo in una stazione secondaria priva di altri oggetti, così da facilitarne il recupero accurato.
• Organo di presa (End-effector): la scelta corretta dell’end-effector è cruciale per aumentare la probabilità di prelievo riuscito in scenari complessi.
• Design del contenitore: il design del contenitore è fondamentale; per alcune applicazioni, una forma a tronco di piramide rovesciata può rappresentare una soluzione efficace.
• Approccio strato per strato: scansionare e prelevare gli oggetti più adatti, quindi effettuare una nuova scansione per avviare l’iterazione successiva, procedendo strato dopo strato.
• Agitatore per contenitori (Bin Shaker): utilizzare un agitatore per modificare la posizione degli oggetti all’interno del contenitore.
• Prelievo a due fasi: prelevare inizialmente l’oggetto nel modo più efficace possibile, per poi separarlo in una stazione secondaria priva di altri oggetti, così da facilitarne il recupero accurato.
• Organo di presa (End-effector): la scelta corretta dell’end-effector è cruciale per aumentare la probabilità di prelievo riuscito in scenari complessi.
• Design del contenitore: il design del contenitore è fondamentale; per alcune applicazioni, una forma a tronco di piramide rovesciata può rappresentare una soluzione efficace.
Precisione di prelievo non ottimale
Nonostante le capacità dei sistemi di visione avanzati, la precisione di prelievo potrebbe non raggiungere sempre il 100%. Gli oggetti posizionati sul fondo, ai bordi o negli angoli del contenitore possono rimanere non prelevati a causa della loro posizione. In questi casi, l’utilizzo di un agitatore per contenitori (bin shaker) per riposizionare gli oggetti in aree più accessibili all’interno del contenitore può rappresentare una soluzione efficace.
Spazio di lavoro limitato e alta velocità del robot
In spazi ristretti in cui è necessario un movimento robotico ad alta velocità, l’utilizzo di un software di pianificazione del movimento è fondamentale. È spesso necessario disporre di un file CAD leggero dell’area di lavoro e dell’end-effector, che includa anche il modello del robot, al fine di simulare le traiettorie potenziali e calcolare il percorso più sicuro.
Oggetti trasparenti o lucidi
Gli oggetti trasparenti o metallici lucidi presentano ulteriori sfide nella generazione di una nuvola di punti accurata per il posizionamento del punto di prelievo. Le soluzioni includono l’impiego dell’IA, di tecniche di visione artificiale e di pre-elaborazione delle immagini, oltre all’utilizzo di uno scanner 3D di alta qualità. La combinazione di metodi come la visione stereo e la proiezione strutturata della luce, insieme alla possibilità di selezionare colori di luce diversi, alta risoluzione e maggiore intensità luminosa, può contribuire in modo efficace a superare queste difficoltà.
Prelievo casuale da contenitori tramite IA
L’IA è fondamentale per ottenere un rilevamento di alta qualità e un posizionamento preciso dei punti di prelievo, mantenendo al contempo tempi ciclo competitivi nelle applicazioni industriali. Quando combinata con tecniche di visione artificiale e di pre-elaborazione delle immagini, l’IA può adattarsi a diverse condizioni ambientali e orientamenti degli oggetti. Questa adattabilità rende l’IA particolarmente adatta alle applicazioni di prelievo casuale da contenitori, dove gli oggetti sono disposti in modo irregolare. I modelli IA sviluppati per questi scenari devono essere robusti e flessibili, in grado di affrontare sfide di prelievo complesse e diversificate.
Il prelievo casuale da contenitori, potenziato dall’IA e da sistemi di visione avanzati, sta trasformando l’automazione industriale in numerosi settori. Scopri come le soluzioni di visione 3D e IA di Solomon possono ottimizzare le tue operazioni.