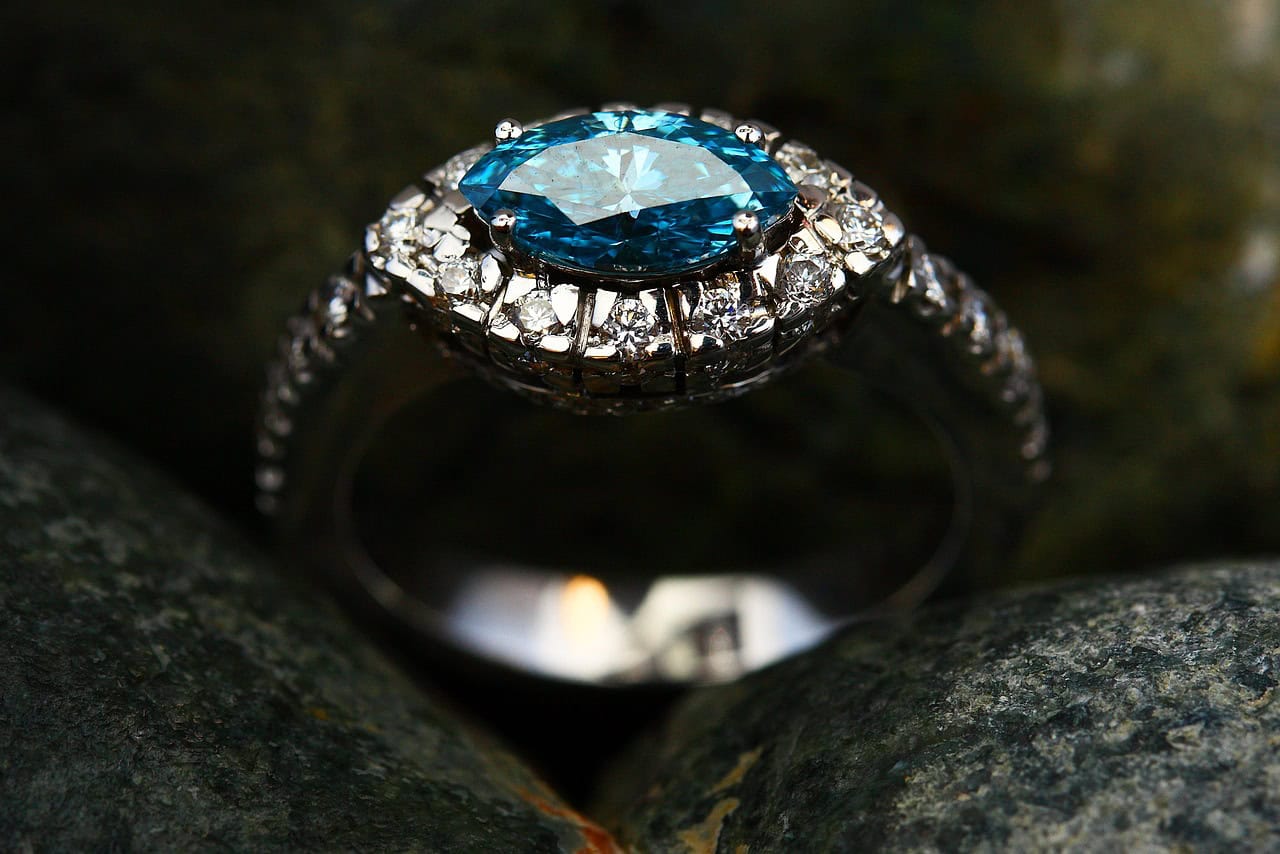
AccuPickCase Study
Automated Fragile Goods Handling Using AI
Customer
The client is a leading luxury brand specializing in crystal glass, jewelry, rhinestones, watches, and accessories. They partnered with a third-party logistics (3PL) provider to automate fragile goods handling and improve order fulfillment efficiency. The 3PL provider aimed to eliminate manual handling of delicate items to reduce errors, prevent damage, and streamline operations at their logistics hub.
Challenge
Automating Fragile Goods Handling
The 3PL provider needed to enhance their order fulfillment by automating the handling of fragile goods. The challenge was to replace the manual process of transferring and verifying delicate items, such as high-end crystal accessories, with a robotic system. The solution required technology capable of accurately distinguishing between variously sized and densely packed packages, while also ensuring that delicate products were handled with the utmost precision to prevent damage during picking and placement.
Solution
Enhancing Fragile Goods Handling with AccuPick
To address the need for efficient fragile goods handling, the 3PL provider conducted a blind test of various vision systems using Azure Kinect cameras and Omron robots. Solomon’s AccuPick emerged as the top solution due to its advanced AI-driven algorithms and 3D imaging capabilities. The system employed high-accuracy instance segmentation to identify and manage packages in densely packed bins, ensuring precise handling of fragile items. AccuPick’s sophisticated motion planning facilitated the safe placement of packages through advanced path analysis and collision avoidance. The solution also offered seamless integration with various end-effectors, automatically selecting the most suitable gripping method for each package to ensure both packaging and contents were handled safely and efficiently.