AI 與 AOI 差異在哪?優缺點與應用有那些?
訂單從過往「少樣多量」變成如今「多樣少量」的彈性生產,待測物件尺寸、外型、材質等複雜度隨之提高,甚至出現定義不明的瑕疵,而傳統 AOI 需先定義瑕疵樣本,並以設定好的參數做為判斷基準,無法靈活快速做出判斷,導致漏檢率大幅增加,在此情況下,AI 崛起讓機器視覺開始進化,其「擬人化」技術便成為新解方。
AOI 檢測系統成為工業製程上瑕疵辨識的應用主流
隨著消費性電子產品不斷推陳出新,帶動半導體、面板、光電、能源、通訊等製造業發展,產品檢測方式也迎來了質變。由於任何零組件的瑕疵都可能影響產品功能,因此製造業對於提升良率需求與日俱增。傳統產線仰賴大量人工檢測產品瑕疵模式,已無法滿足產品全檢與生產效率需求,因此導入 AOI 自動光學檢測系統成為工業製程上瑕疵辨識的應用主流,點此了解甚麼是 AOI 與其優點。
AOI 系統以機器視覺為核心,結合光學、電控、機構以及檢測軟體執行檢測作業。透過光源配置凸顯影像特徵,輔以電腦影像處理技術進行定位及檢查,快速篩檢產線中成品、半成品的缺陷、污染物及其他異常。相對於人工檢測,AOI 系統對於瑕疵判定的標準較為一致。此外,搭載高解析度相機的 AOI 系統能檢測人眼難以辨識的細節,每分鐘數以千計的篩檢量能也改善傳統人工目視檢測效率不彰的缺點。
AOI 瑕疵檢測在製造業上應用極為廣泛
AOI 在製造業的應用極為廣泛,舉凡檢查產品上有無變形、破損、缺件、髒污與刮痕等瑕疵,或者是讀碼、對位、精密測量、印刷檢驗(如圖1),皆能透過 AOI 技術進行檢驗,因此如半導體、印刷電路板(PCB)、面板、電子機械、紡織、食品加工、汽車等產業,都能看見其蹤影,其中更以 PCB 和面板產業為大宗。
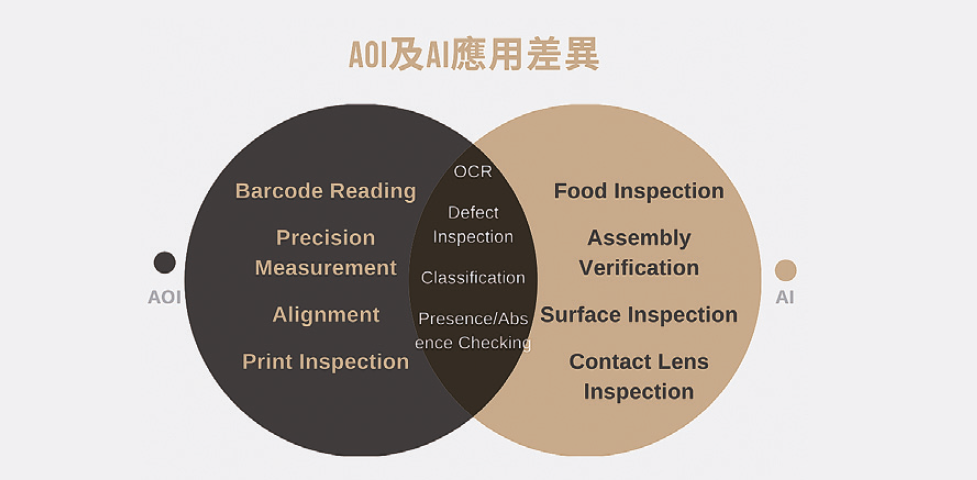
AOI 不具 AI 自主學習能力,面臨檢測痛點
儘管 AOI 系統已廣泛應用於各製造業產線,但其必須高度客製化的特性仍造成導入的難度與限制,面對複雜的產品瑕疵、影像背景、光影變化,AOI 系統使用相對受限。
AOI 採用 Rule-based 判斷機制,透過程式語言撰寫檢測邏輯(Rule),僅能以定義好的參數作為基準檢測樣本瑕疵。舉例而言,檢測邏輯將瑕疵定義為圓形,非屬圓形的瑕疵便無法透過 AOI 系統檢測出異常,因此常產生漏檢(Leakage)問題,諸如蛋殼孔樣貌不同、PCBA 異常瑕疵檢測、塑膠扣具瑕疵檢查的脫模劑油汙、金屬沖壓件刮痕檢查等隨機生成的瑕疵類型,都是 AOI 系統的剋星。
為求避免瑕疵漏檢情形,AOI 系統往往將參數設定得相對嚴格,導致系統過於敏感,易受光影等外在條件影響而造成誤殺(Overkill)現象。除工程人員必須不斷調整演算法及參數外,產線亦須配置人員重複檢測產品以避免漏檢、誤殺情形,大幅影響生產效率且提高生產成本。
AOI 相當依賴光源、相機、鏡頭三者間的密切搭配。以光源來說,為了強化對比以呈現物體特徵,需根據待測物件材質、顏色、形狀設計光線強度與特性,藉以取得適用的影像降低誤殺風險;選擇相機時需依據檢測需求決定感光元件、解析度、幀率等並搭配合適鏡頭,方能發揮光學系統功能,可謂「牽一髮動全身」。
除了設備細節影響成像外,若再遇上調機、更換零組件等情況,則須指派工程師依據經驗值重新進行機台參數設定、對位,再加上軟硬體調整過程相對複雜,維修時間短則幾日長則數月,難以因應智慧製造產線彈性化需求。而這也是為什麼,使用 AOI 的製造廠商,近年紛紛導入人工智慧(Artificial Intelligence, AI)以提升檢測效率的原因,點此瞭解更多 AOI 結合 AI 的優點。
AI 瑕疵檢測助攻 AOI,智慧製造轉型關鍵
AI 深度學習技術的瑕疵檢測與傳統 AOI 最大不同之處,即是經驗法則。AI 好比一位新進的學徒,在一定程度上能夠模仿老師傅的檢測能力,經由運用大量有效資料並透過深度學習技術在系統模型快速訓練,能自行定義出瑕疵範圍與異常偵測模型,自動找出最佳 OK 與 NG 參數,進一步有效判斷未知瑕疵,確保檢驗標準的一致性,大幅提升辨識準確率 ( 如圖2 )。
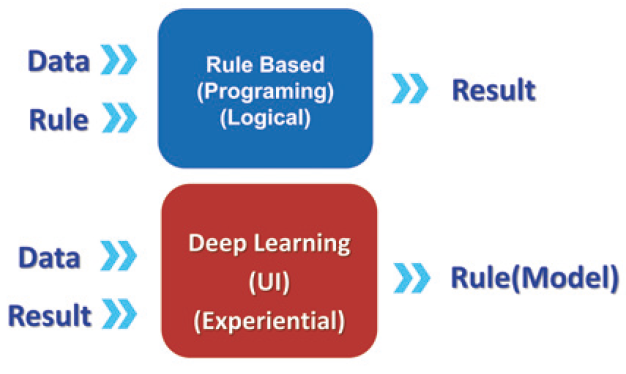
由於各產業 Domain knowledge 差異大,傳統 AOI 工程師協助產業開發 AOI 系統,無法快速解決實際場域問題,因此有賴與具有行業經驗工作人員來回溝通,才能設計適合的 AOI 硬體及 AOI Rule。而 AI 瑕疵檢測系統則是透過介面得知影像中哪些特徵型態為檢測所需,經過學習後,系統便能自行產生檢測 Rule,兩者在學習效率與執行力上有一定差異。
當然,使用深度學習優化檢測準確度外,AI 技術大幅降低檢測效果受光源影響問題。傳統 AOI 常受限於光線、取像角度、陰影反光、待測物件材質及外型(如半透明材質或金屬曲面)等條件,無法精準取得辨識結果,而 AI 瑕疵檢測對光源依賴性小,只要光源穩定,即使輪廓、形狀較為模糊,甚至金屬材質反光所造成的干擾,AI 仍可進行檢測分類。
AI 瑕疵檢測擅長解決複雜的表面和外觀缺陷,比如反光物件上的凹痕和刮痕(如下方案例研究影片),同時,針對變形及不易辨識字元,依舊能實行光學字元辨識(Optical Character Recognition, OCR);另外可篩檢不可預測的圖案與瑕疵,即使瑕疵的顏色大小不一、變形量大、圖形複雜且分散在隨機處,AI 也能依照數據分析判斷瑕疵位置。因此無論分析速度、準確性與人力成本上,基於規則的傳統演算法難以解決的複雜檢測和分類應用,深度學習皆有望克服侷限性。
泡殼包裝 (PTP) 產線每小時約包裝 5,000 ~ 40,000 顆錠劑或膠囊,填充時偶有誤差,造成泡殼內無內容物、內容物不良或膠囊粉末溢出等瑕疵。藉由各種瑕疵類型的影像樣本訓練 AI 模型,可即時且迅速地辨識每一泡殼的包裝及填充情形,並予以標註分類。