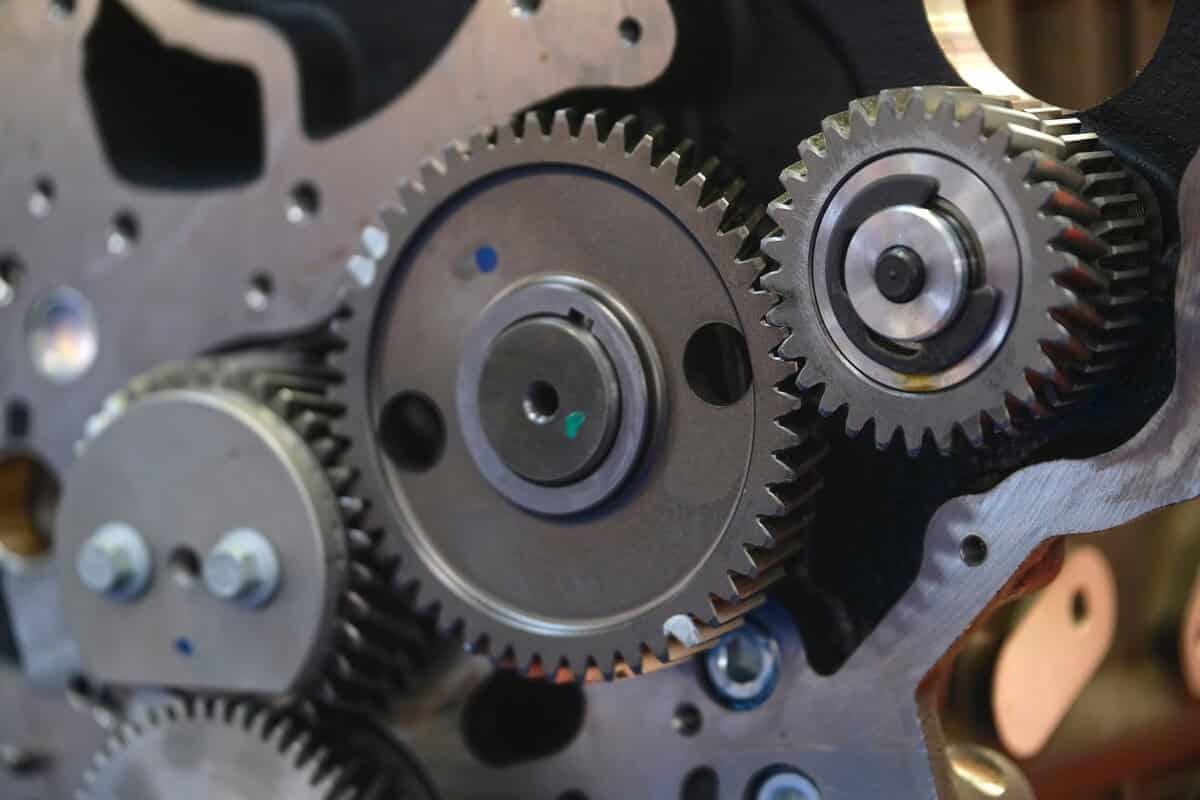
AccuPickCase Study
Automated Gear Loading Using AI
Customer
The customer is a large automotive component manufacturer based in Asia.
Case
Automated Loading in Automotive Component Manufacturing
Automotive component manufacturers have traditionally relied on manual labor for loading tasks. This approach is labor-intensive, particularly due to the large quantity and weight of metal parts like gears. As a result, factors such as site conditions and worker capabilities can lead to fluctuations in loading efficiency. To address these challenges, auto component manufacturers are increasingly adopting automated loading systems to enhance production efficiency and reduce risks associated with manual labor methods.
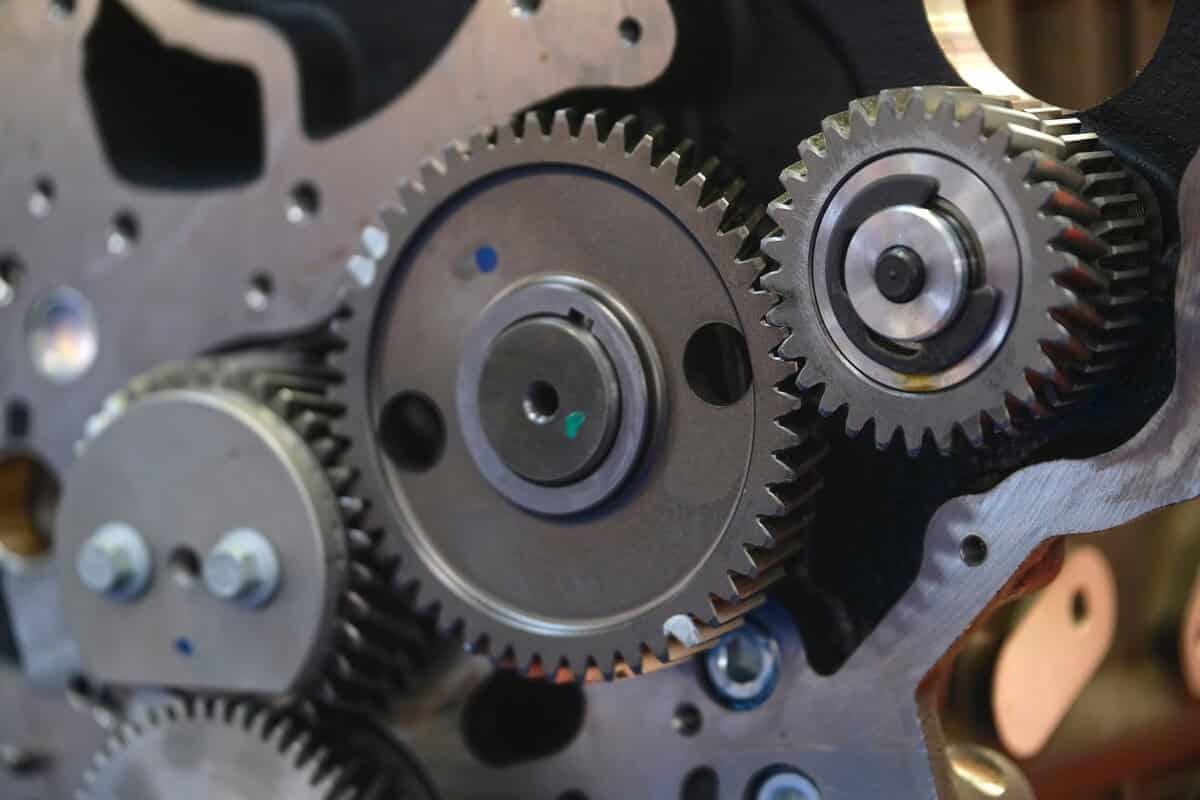
Challenge
Limitations of Ordinary Machine Vision Systems
Two major technologies currently dominate factory automation: (1) the use of industrial cameras placed within the operating area and (2) the use of industrial cameras mounted on robotic arms. These cameras precisely ascertain the relative positions of objects, facilitating the guidance of robotic arms in performing loading and unloading tasks. However, challenges arise in environments where illuminating objects from the side is hindered by environmental lighting interference. Additionally, issues like small gear size, reflective materials, oil contamination, and disordered stacking of workpieces in the bin present significant challenges for ordinary machine vision systems, resulting in inefficiencies in robot arm grasping.
Solution
Automated Gear Loading with AccuPick
Using industrial cameras and advanced AI, AccuPick learns and classifies gear stacking conditions and angles from a small number of image samples. AccuPick’s motion planning module swiftly calculates the optimal robot path, allowing the robotic arm to accurately pick gears from different angles, avoiding collisions with the bin.