客戶
該客戶是亞洲一家大型汽車零組件製造商。
案例
傳統汽車零組件上料模式導入自動化應用
汽車是資本和技術密集型的產業,其涵蓋多個領域,包括零組件製造、整車生產和銷售服務等上中下游供應鏈,因此又被稱為「火車頭工業」。
一輛汽車約由1萬多個不可拆解的獨立零部件組裝而成,而傳統零組件製造商在生產時,多仰賴人力支援物件上料維持生產效能。然而,由於齒輪等金屬零件數量多且具一定重量,勞動強度大,導致上料效率易隨著現場環境、工人身體狀況等因素有所波動。因此客戶正積極導入自動化上料系統,進一步提升生產效率並降低可能風險。
一輛汽車約由1萬多個不可拆解的獨立零部件組裝而成,而傳統零組件製造商在生產時,多仰賴人力支援物件上料維持生產效能。然而,由於齒輪等金屬零件數量多且具一定重量,勞動強度大,導致上料效率易隨著現場環境、工人身體狀況等因素有所波動。因此客戶正積極導入自動化上料系統,進一步提升生產效率並降低可能風險。
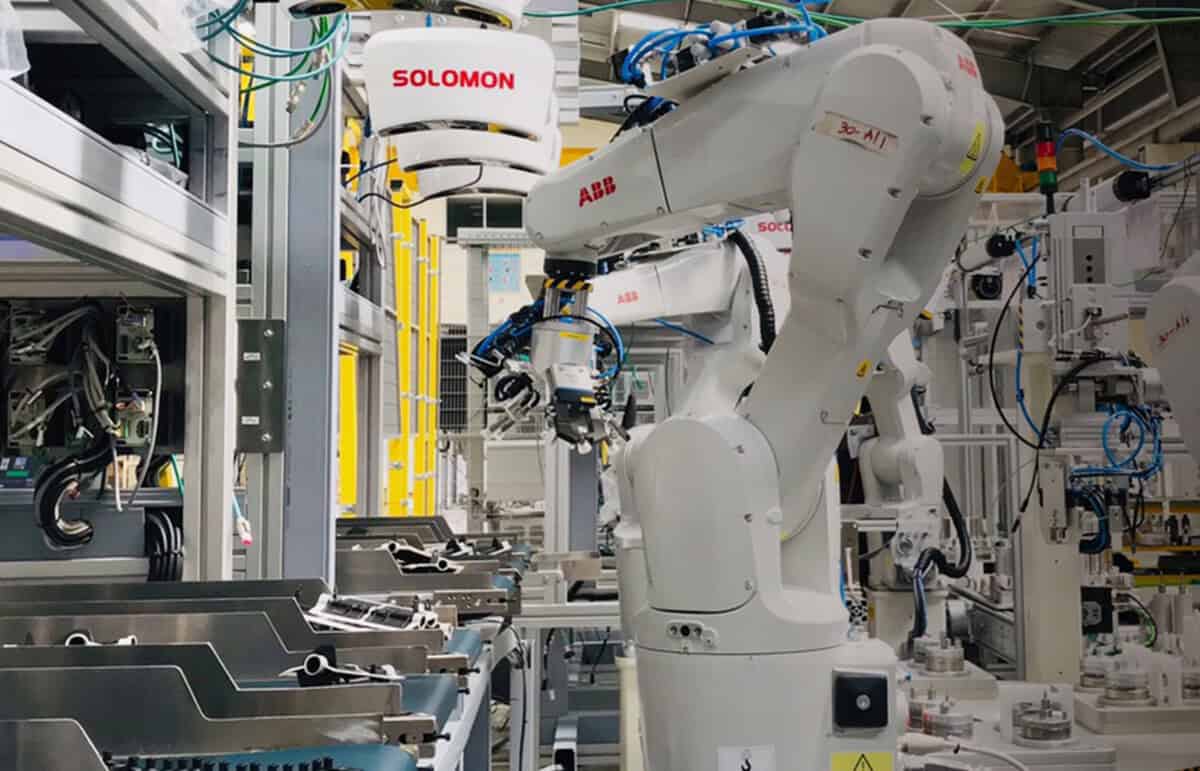
挑戰
需克服零組件角度難以取放與料箱深度問題
運用建置於作業區域與手臂上的工業相機,有效判斷出物件相對位置,再引導機械手臂完成取放動作,是目前工廠自動化中的兩大應用技術。
不過由於廠房環境光源干擾,無法提供被側物特定照明,再加上齒輪體積小、材質反光且裹滿油污、工件無序堆積在料籃中等情況,機器視覺系統識別難度大,導致機器手臂夾取效率不佳。
解決方案
使用 AccuPick 3D 視覺實現自動化內星輪上料
所羅門導入 AccuPick 3D 智能取放系統與機械手臂進行整合,透過工業相機取得少量圖像樣本後,自主研發的 AI 演算法便可進行學習、分類,進而判斷齒輪堆疊狀況與角度,再搭配 AccuPick 3D 內建動作規劃模組(Motion Planning),可在最短時間內計算出最佳路徑,機械手臂可因應實際的料箱堆疊情況,精確地從不同角度進行齒輪拾取,並防止機器手臂與碰撞料箱碰撞的問題。