Bin Picking in 1 Minute with AI and 3D Vision
Introduction to Vision-Based Bin Picking
2D vs 3D Machine Vision
Stereo Vision
Stereo vision mimics human depth perception by capturing both an object’s position and its three-dimensional structure. It offers key benefits, including low energy consumption and cost efficiency, making it an attractive option for industrial applications. However, stereo vision can experience delays, and its effectiveness can be reduced in low-light environments. In addition to its use in robotics, stereo vision is being integrated into AR + AI systems for advanced visual inspection and object recognition.
Time-of-Flight
Time-of-Flight (TOF) technology measures the distance to objects by calculating the time it takes for infrared light to travel to the object and return. This method offers fast processing speeds and is resistant to interference, making it well-suited for dynamic environments. However, while TOF is efficient, its accuracy can be lower than other 3D vision technologies.
Structured Light
Structured light projects distinct light patterns, typically alternating black-and-white stripes, onto objects. The deformation of these patterns as they interact with the object’s surface allows the system to map its shape and capture precise depth information along the Z-axis. This technology is commonly used in applications like facial recognition and quality control, particularly in manufacturing through Automatic Optical Inspection (AOI) systems.
Enhancing Robotic Object Recognition with AI
Integrating AI with 3D vision systems enhances the ability of robots to recognize and manipulate objects with greater precision. This combination allows robots to effectively pick and place irregularly shaped items, ensuring correct orientation and positioning.
In cases involving complex shapes—such as stacking U-shaped metal pieces—3D vision alone may fail to accurately align and position the objects. AI fills this gap by enabling the system to understand the objects’ true shape and orientation, ensuring precise handling.
Train an AI Model in 60 Seconds
Solomon’s deep learning AI, combined with advanced motion planning modules, enables robots to learn to identify and interact with objects in as little as 60 seconds. This allows the bin picking system to quickly determine the optimal path for grasping and placement while avoiding obstacles, ensuring accuracy and efficiency.
This powerful integration offers a practical, cost-effective solution for complex tasks like mixed depalletizing, kitting, packing, and random bin picking, making it an ideal fit for dynamic industrial environments.
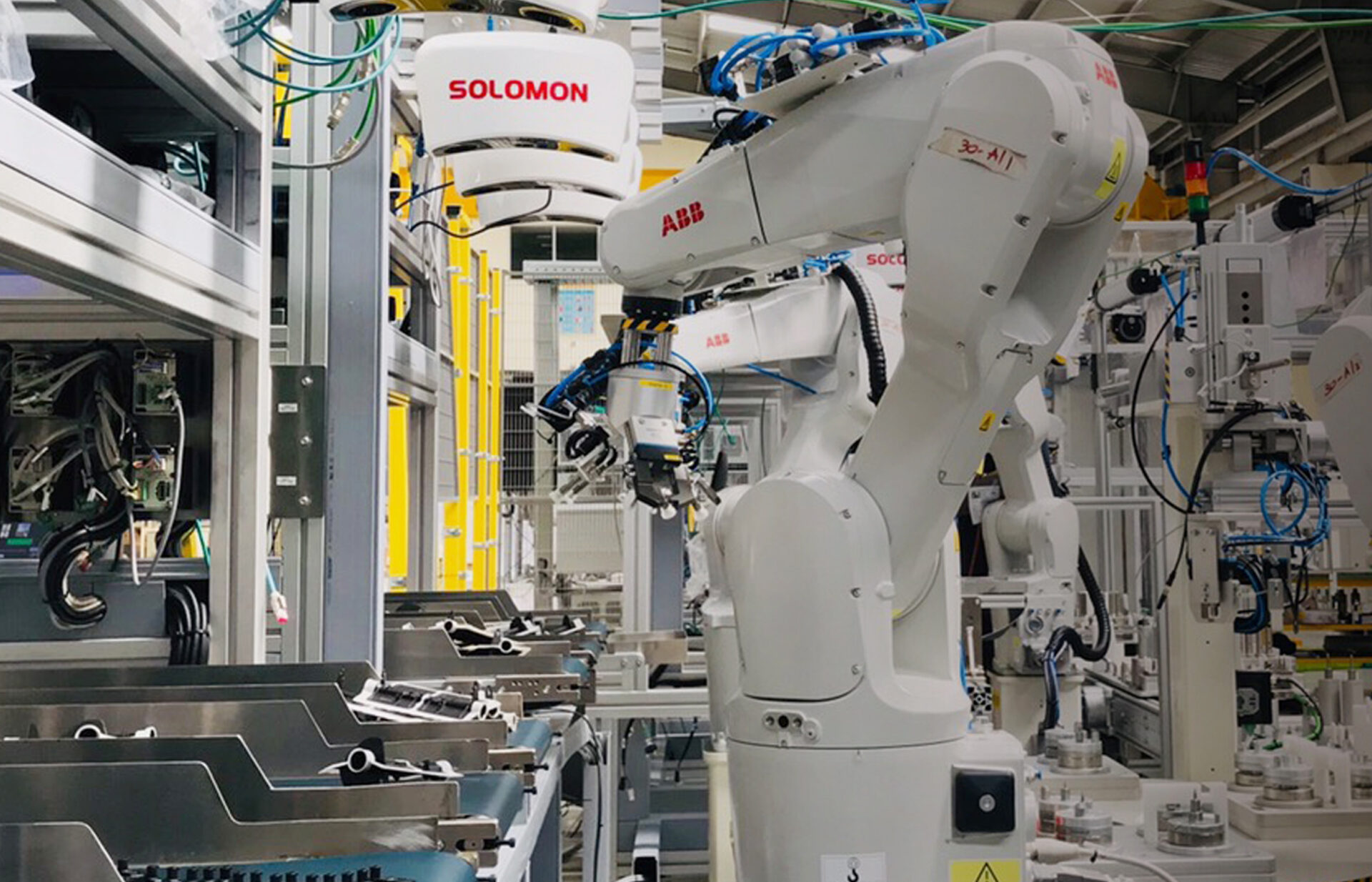