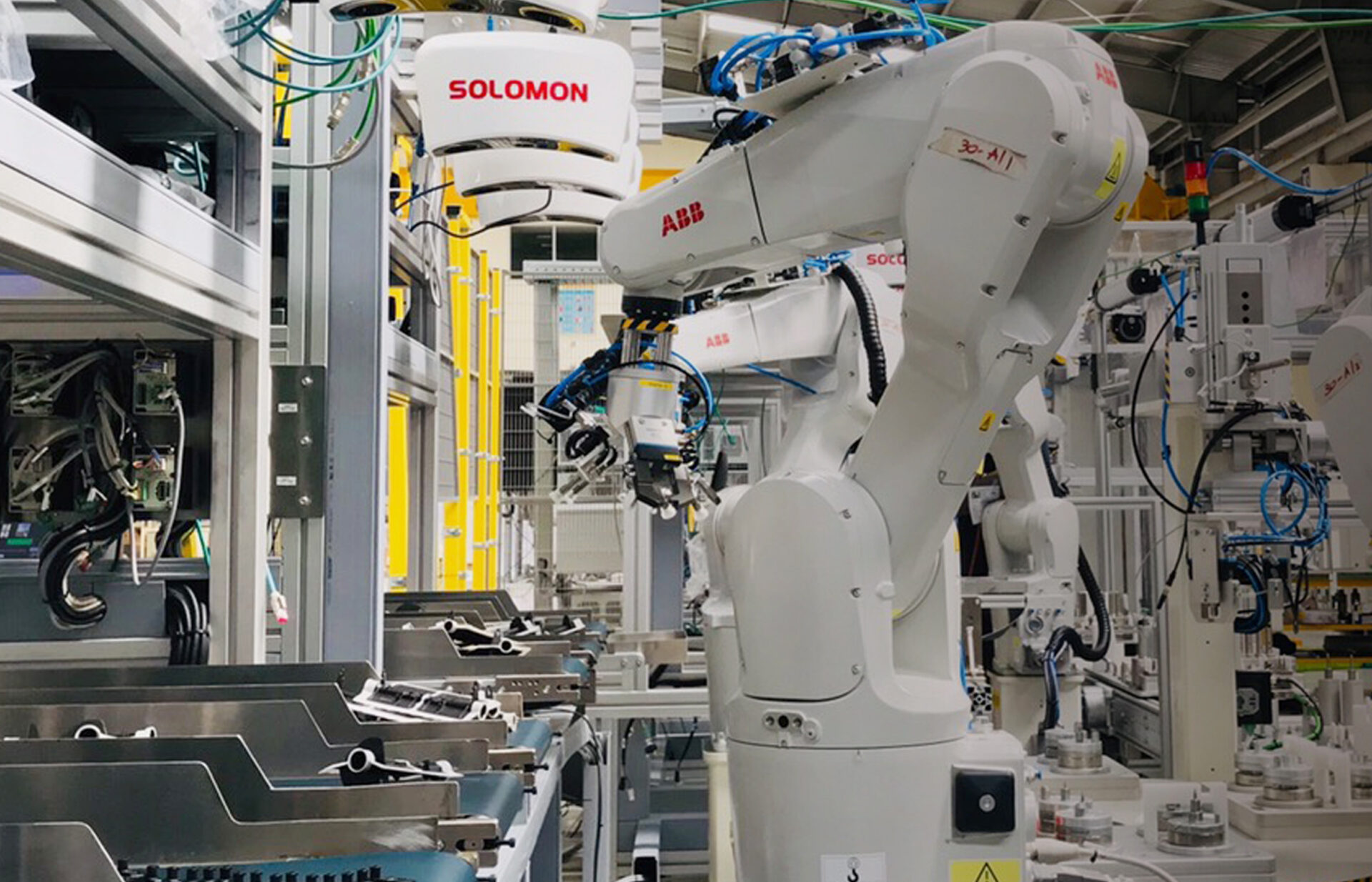
AccuPickCase Study
Automated Assembly Line Using AI
Customer
The customer is a prominent European parts manufacturer specializing in automotive components, particularly air conditioning systems. Their production line operates exclusively for one of Germany’s top automobile brands, ensuring high-precision assembly and quality control in alignment with stringent automotive standards.
Challenge
Fully Automated Kitting and Assembly Line
The customer aimed to implement a fully automated kitting and assembly line but faced significant challenges. Limited workspace constrained the arrangement of multiple robot arms due to bulky vibrating mechanisms and outdated 2D vision systems. This hindered efficient automation. Additionally, handling a large number of intricate assembly parts required extensive custom mechanical design and constant fine-tuning of the 2D vision system. The project demanded precise coordination among multiple robots operating on separate conveyors to execute ready-to-pick tasks simultaneously and with high speed, essential for achieving the automation efficiency the customer sought. The customer needed a solution that integrated AI to overcome the limitations of traditional systems and improve both speed and precision in the assembly process.
Solution
AccuPick Optimizes Automated Assembly and Kitting
We integrated three vision scanners with multiple robot controllers, streamlining the automated assembly line and optimizing space utilization within just 1 sqm. Using AccuPick, Solomon’s AI-powered 3D bin picking software, and SolScan, an industrial 3D camera, the system accurately recognized and picked intricate, overlapping components with less than 1 mm tolerance. This AI-driven solution reduced cycle times to under 5 seconds per component, with recognition in less than 2 seconds. Our multi-functional gripper design enabled multiple robots to handle and place various components simultaneously, accelerating kitting and improving assembly line efficiency.
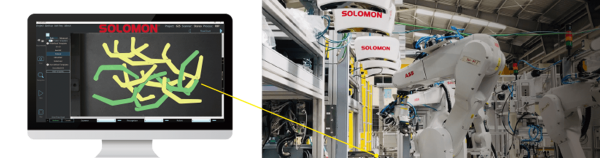