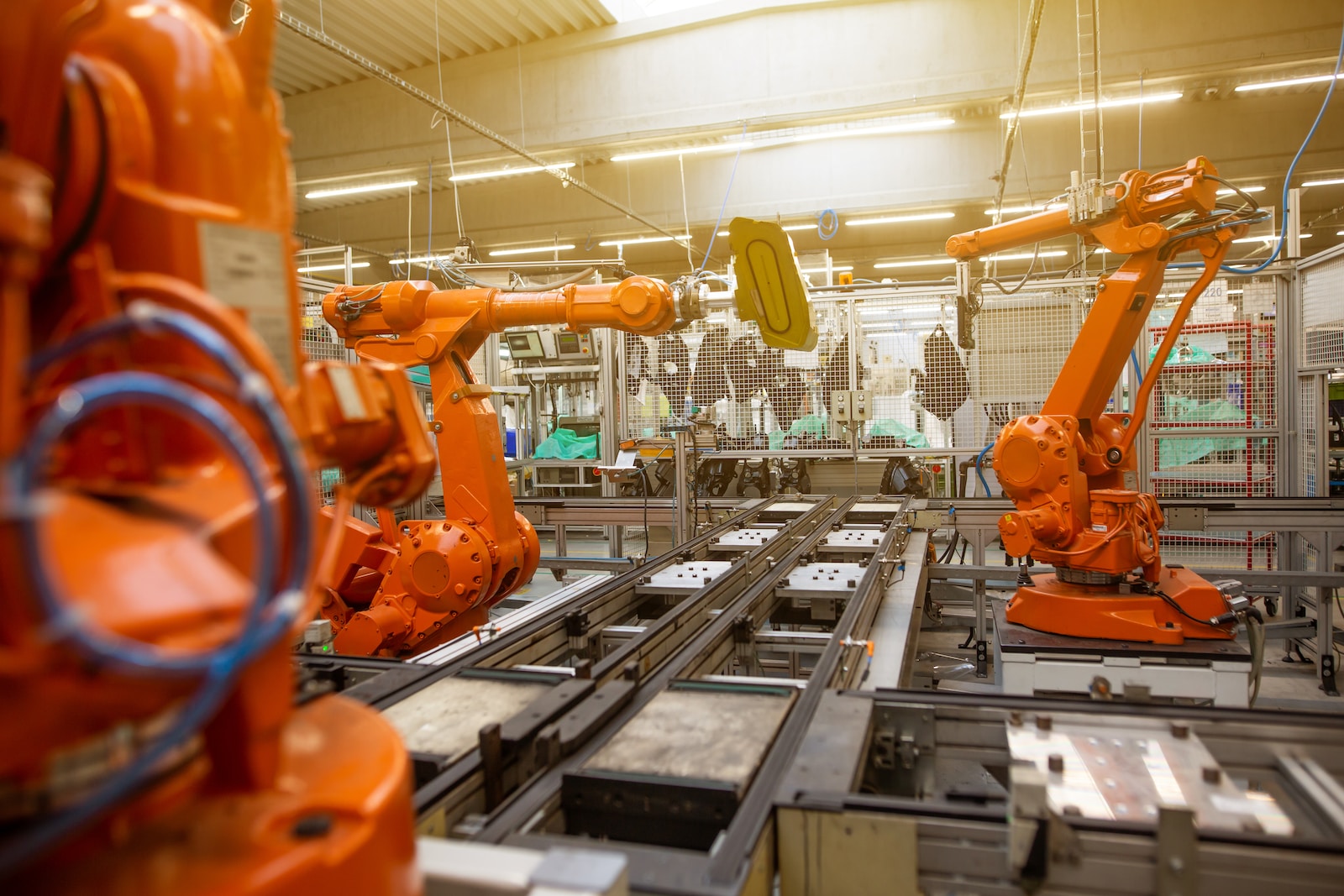
AccuPick成功案例
套件及组装产线自动化
客户
该客户是欧洲知名汽车零组件制造商,其生产线专门为一家德国领先的汽车制造商生产空调。
挑战
客户希望在有限的空间及复杂零组件条件下,建立一条全自动化的物料组装生产线
然而,这样的期望,却受限于笨重的振动机构和 2D 视觉系统所需的庞大运作空间,要能在有限办公场域中再增添更多机械手臂,有相当程度的执行难度。
此外,因应大量复杂组件,过程中需导入 2D 视觉系统的微调及精密机械协作,以利生产线的完善,有鉴于此,该项目要求能在独立输送带中同时进行多机械手臂精准协作,迅速执行待处理的任务。
解决方案
所罗门的 3D 视觉系统,能有效优化装配线流程并使空间利用率最佳化
所罗门将三个视觉扫描仪与机器人控制器进行集成,满足输送带上高速多组件处理需求后,同时更释放额外设备所占的空间,从而改善装配线流程。
此次解决方案,搭载所罗门 AccuPick 3D、所罗门 AI-based 3D 料箱拣选程序和结构光扫描仪 SolScan,在精准识别复杂物体上有着优异表现。搭载所罗门解决方案,机器手臂能有效在重叠、复杂物体中辨识正确的抓取点,并满足小于 1 毫米的严格公差要求。
透过高速结构光扫描仪与先进的 AI 算法,所罗门智能取放系统将每个组件的循环时间显著缩短至 5 秒以下、快速辨识功能每个零件仅需不到 2 秒。
此外,透过所罗门多功能夹爪设计可进一步简化操作,同时能处理 2 至 3 种不同元件并准确地放置在指定装配位置,让机器人轻松执行捡取和放置任务,进一步减少循环时间。
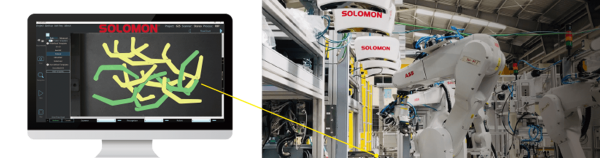