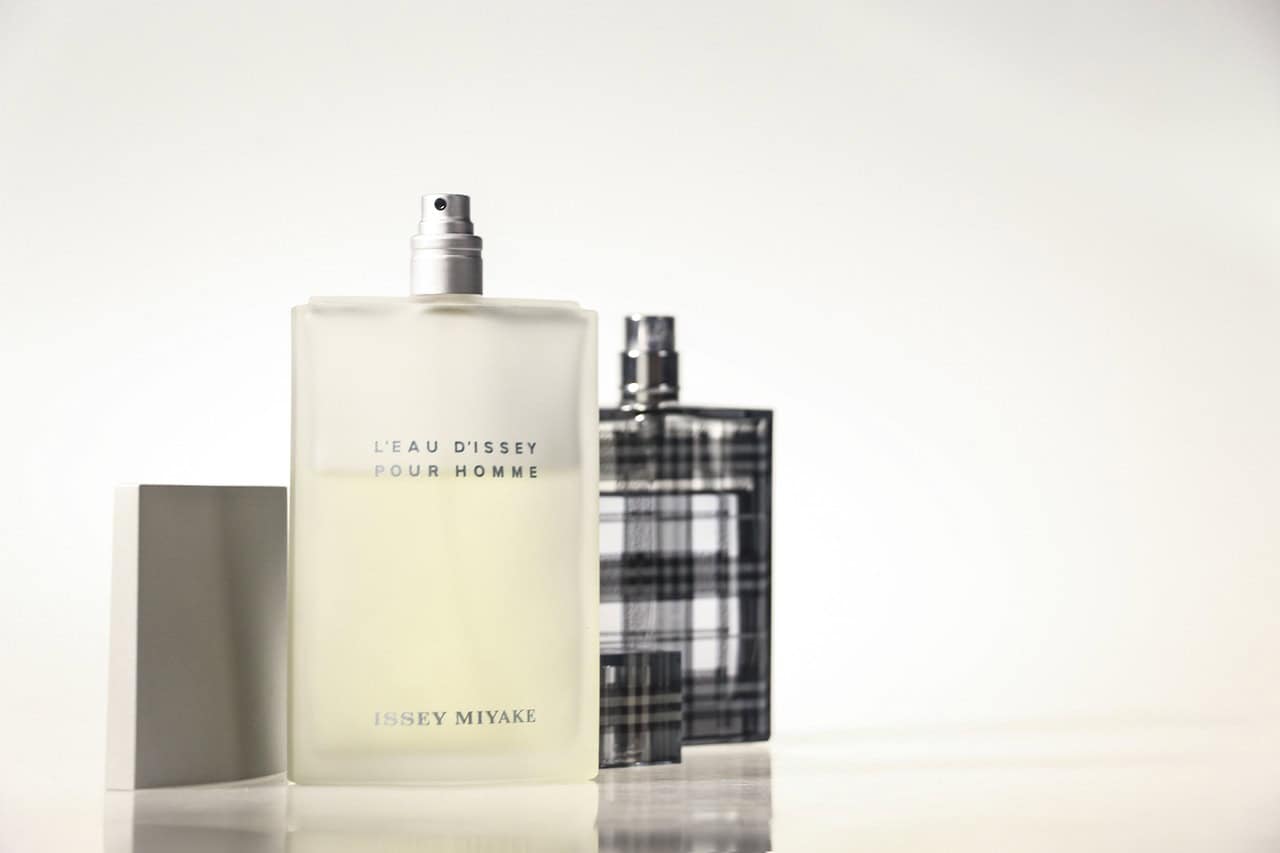
SolVisionCase Study
Glass Bottle Inspection Using AI
Case
Translucent Glass Bottle Quality Control
Translucent glass bottles, often created using gradient-colored techniques, feature a distinctive matte finish achieved through high-pressure air jets that apply mist particles to the glass surface. Known for their aesthetic appeal, these bottles are produced using two primary methods: internal sandblasting and external sandblasting. The gradient effect not only enhances the visual design but also adds a unique translucent quality to the glass.
Challenge
Defining Defects on Gradient-Colored Glass
Gradient-colored glass often exhibits uneven spots and imperfections resulting from the sandblasting process. These defects vary in color, size, and location, making it challenging to establish a clear definition or standardized criteria for what constitutes a defect. Consequently, traditional logic-based inspection methods are ineffective for accurately identifying and assessing these imperfections.
Solution
Precise Inspection with SolVision
SolVision leverages advanced image processing to automate the inspection of gradient-colored glass bottles, effectively identifying production flaws. Utilizing its Segmentation tool, the system learns to recognize defects through sample images. Once trained, the AI model can swiftly detect and categorize defects based on location, angle, and size distribution during production, ensuring precise and efficient quality control.
Glass Bottle Inspection


Fragrance Bottle Defect Detection