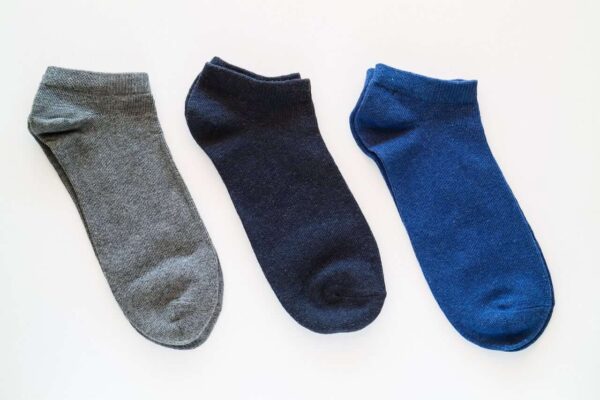
SolVisionCase Study
Socks Defect Detection Using AI
Customer
The customer is a leading sock manufacturer aiming to enhance quality control and operational efficiency through AI-powered visual inspection.
Case
AI Visual Inspection of Socks
The sock manufacturing process consists of several key stages: design, knitting, sewing, shaping, inspection, and packaging. In this labor-intensive industry, quality control is often performed manually at various checkpoints. Unfortunately, relying on human inspectors can lead to low detection rates for socks defects, as visual fatigue commonly affects workers. This inefficiency not only slows production but also increases the risk of compromised product quality.
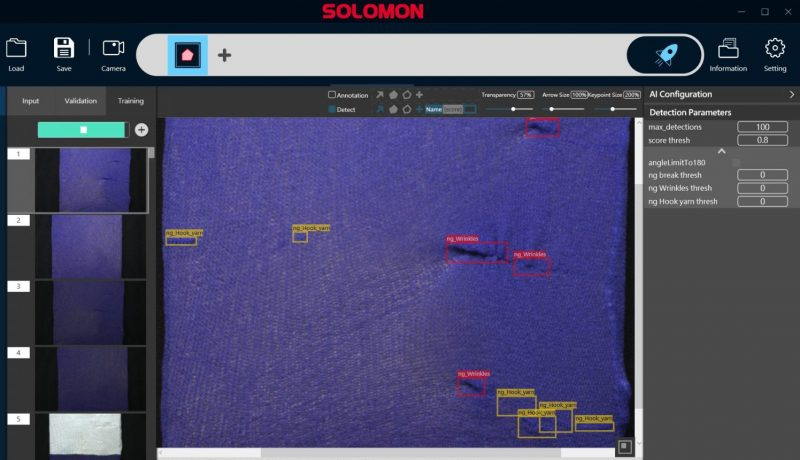
Challenge
Traditional Inspection Methods Limitations
Socks are susceptible to various defects, including sewing faults, holes, and rips, which can differ in size and location. While traditional rule-based vision systems can inspect entire pieces of fabric, they often struggle to detect irregular socks defects. This limitation in defect detection typically necessitates additional manual checking, further reducing efficiency and increasing the risk of missed detections. To address these challenges, there is a pressing need for advanced AI-powered defect detection solutions that can enhance accuracy and streamline the inspection process.
Solution
Real-Time Defect Detection with SolVision
SolVision, Solomon’s AI-powered defect detection system, is trained using a small set of sample images to identify defective socks in real-time. The system excels at quickly and accurately recognizing various socks defects, classifying them to ensure that faulty products do not proceed through the production line. By analyzing defects in real-time, SolVision helps safeguard product quality while significantly improving production efficiency.
Socks Defect Detection and Classification
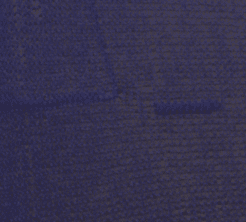
Needle Mark
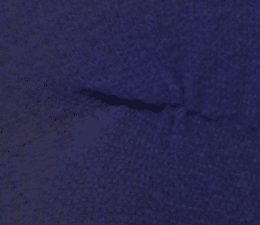
Seam Puckering
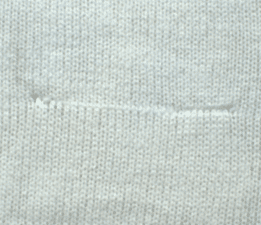
Needle Mark
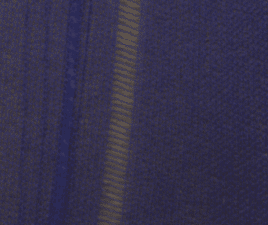
Broken Needle