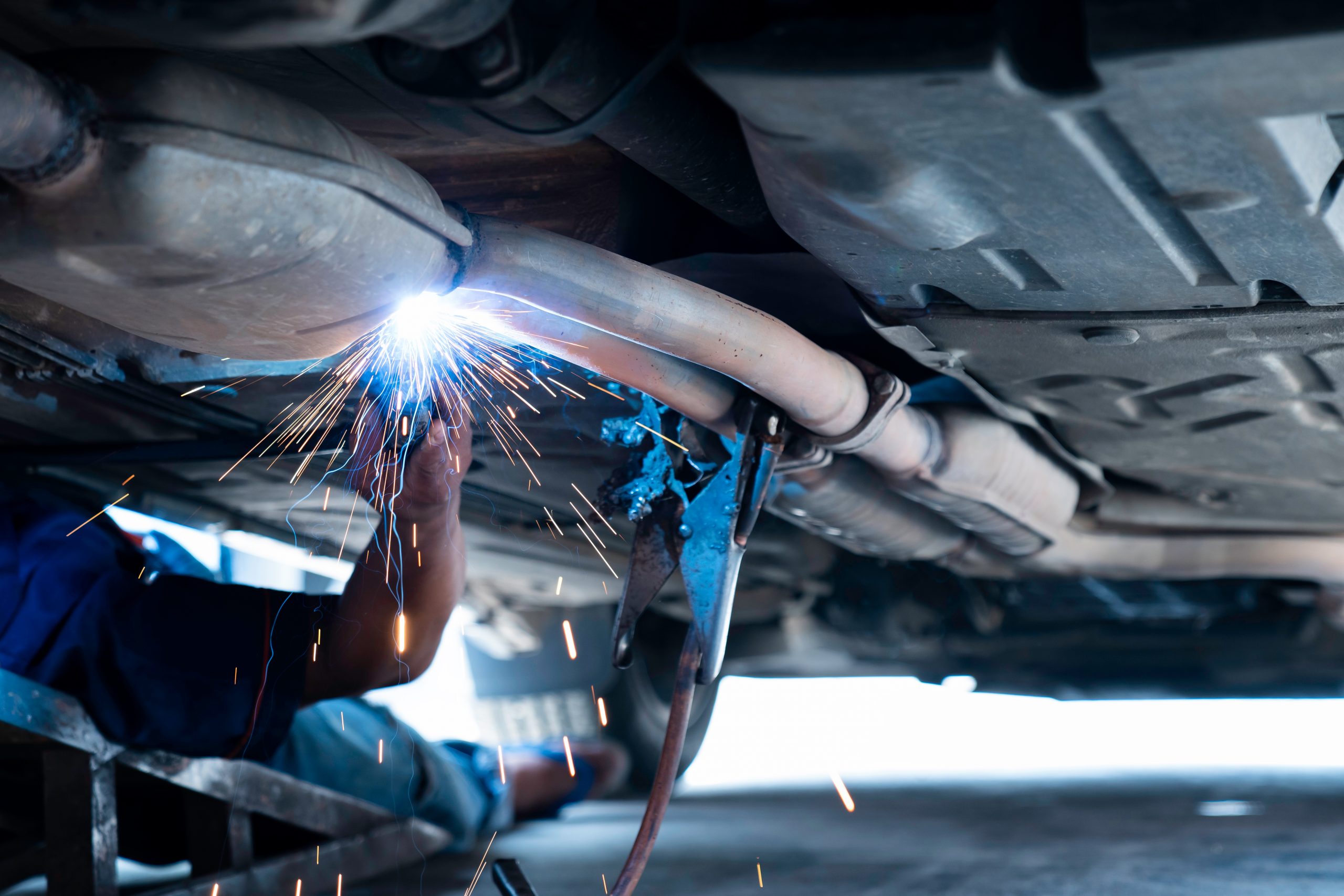
META-aiviCase Study
Welding Bead Defect Detection Using AR + AI
Customer
The customer is a car manufacturer based in Asia.
Case
Challenges in Examining Welding Quality
Cars have multiple complex surfaces and features, leading to variations in welding locations and techniques. The examination of automotive welding quality requires inspection from multiple angles due to the irregular shape of the vehicle chassis and body panels. Automating this process is challenging and costly, leading to a reliance on manual inspection. However, if personnel are careless in their inspection, defective products may enter the market, posing a risk to driving safety.
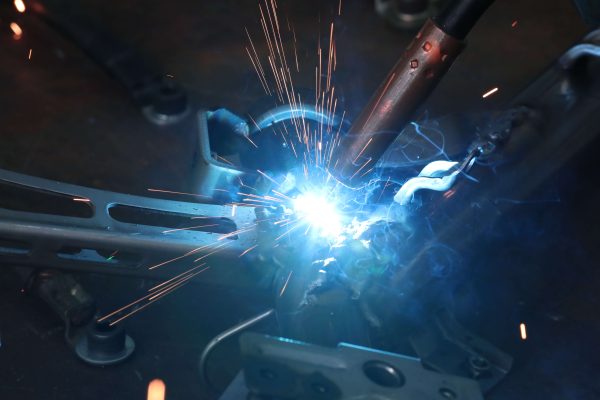
Challenge
Limitations of Manual Inspection for Irregular Defects in Automotive Welding
Manual inspection of automotive welding quality can lead to irregular defects being overlooked. Despite advanced welding techniques, ensuring flawless welding remains challenging. Frames have multiple inspection points and multi-faceted features, making manual inspection the current reliance, but inconsistent quality is a concern.
Solution
Enhancing the Accuracy of Manual Inspection with META-aivi
By utilizing the defect detection function of META-aivi, AI models can be trained and uploaded into the system for qualified welding points. This enables AI inspection of welded sections using AR glasses or a tablet device to quickly recognize defective welds. Augmented reality feedback is provided in real-time, allowing personnel to correct errors through onscreen instructions, ensuring welding quality. META-aivi can also distinguish between types of defects such as incomplete welding, sand holes, carbonization, and spatter. For example, if sand hole defects are continuously detected, it suggests a need to replace welding wires, while frequent incomplete welding cases may require nozzle inspection. The accumulated data can be used for subsequent big data analysis and maintenance purposes. In addition, product inspection histories can be outputted, effectively digitizing the inspection process.
META-aivi Inspection Results
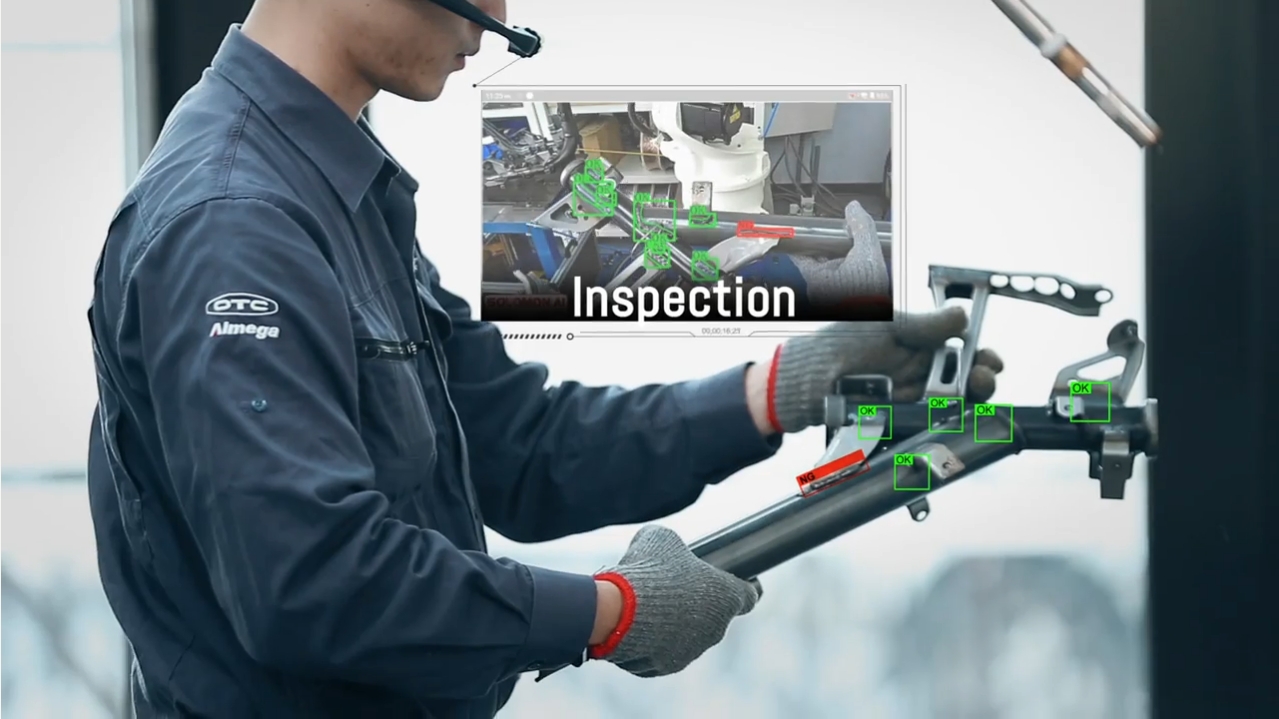
During AI inspection META-aivi detects any welding defects
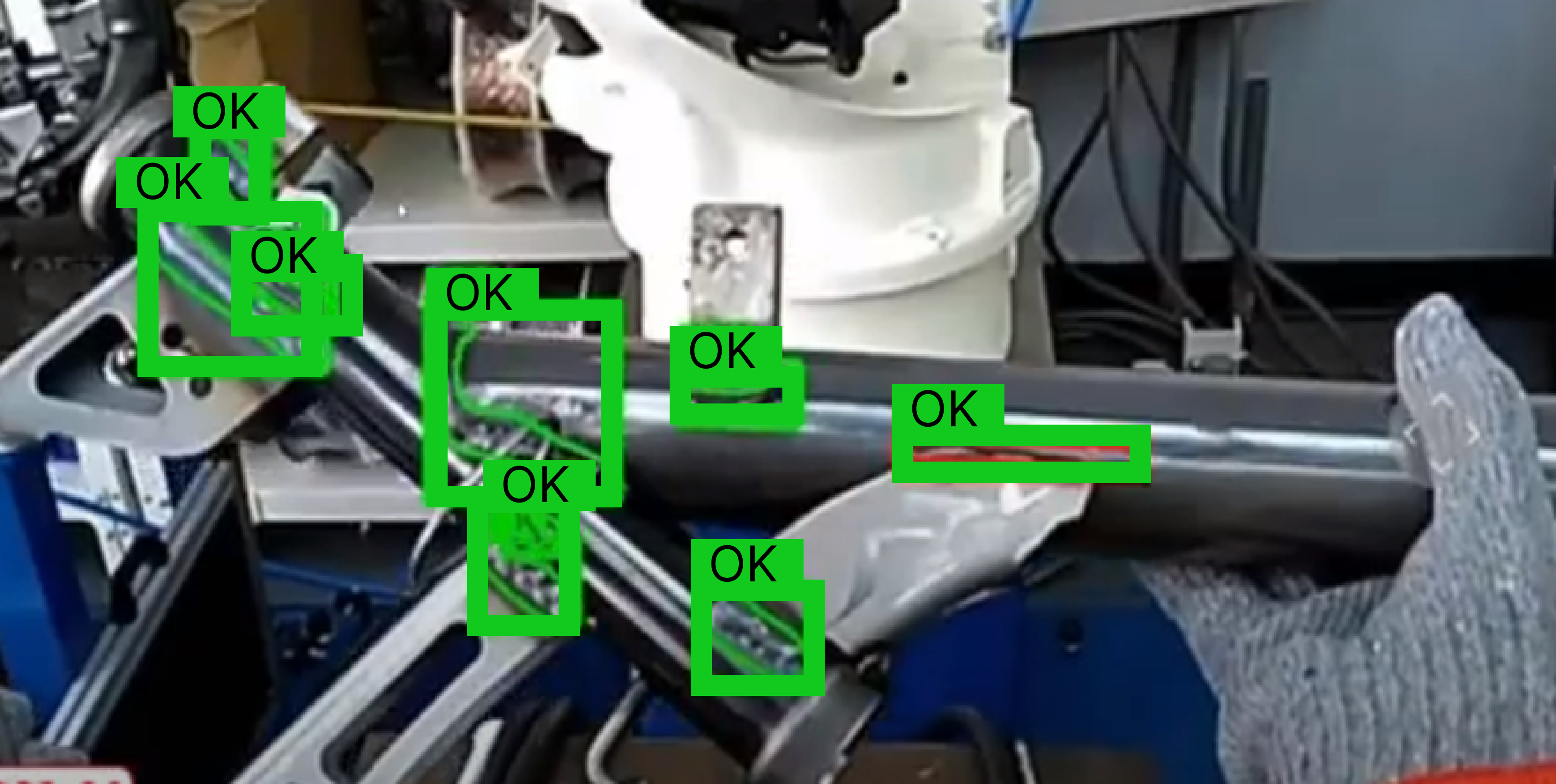